Ποιοι είναι οι παράγοντες που επηρεάζουν την παραγωγή μπρικέτες από άνθρακα καρύδας;
Για την επεξεργασία υψηλής ποιότητας και κανονικού σχήματος μπρικέτες άνθρακα καρύδας, χρησιμοποιούνται συνήθως εμπορικές μηχανές μπρικέτας με κάρβουνο με κέλυφος καρύδας. Όταν παράγουμε μπρικέτες με κάρβουνο καρύδας, δεν πρέπει να προσέχουμε μόνο τη σωστή χρήση τους μηχανή κατασκευής μπρικέτες με κάρβουνο αλλά και δώστε προσοχή σε διάφορους παράγοντες που επηρεάζουν την παραγωγή μπρικέτες από κάρβουνο καρύδας. Μόνο με το χειρισμό της ανάμειξης του συνδετικού υλικού της σκόνης ξυλάνθρακα, της υγρασίας της σκόνης ξυλάνθρακα, της ομοιόμορφης παραγωγής και άλλων παραγόντων, μπορούμε να παράγουμε υψηλής ποιότητας μπρικέτες ξυλάνθρακα.
Τι είναι μια μηχανή μπρικέτας με κάρβουνο καρύδας;
Η μηχανή μπρικέτας άνθρακα καρύδας ονομάζεται επίσης μηχανή εξώθησης μπρικέτας ξυλάνθρακα με κέλυφος καρύδας, η οποία χρησιμοποιείται κυρίως για την εξώθηση σκόνης άνθρακα από κέλυφος καρύδας σε διάφορα σχήματα μπρικέτες άνθρακα. Συνήθως, χρησιμοποιούμε τη μηχανή μπρικέτας με κάρβουνο με κέλυφος καρύδας για να επεξεργαζόμαστε κάρβουνο ναργιλέ σε σχήμα μπλοκ και εξάγωνο κάρβουνο μπάρμπεκιου.
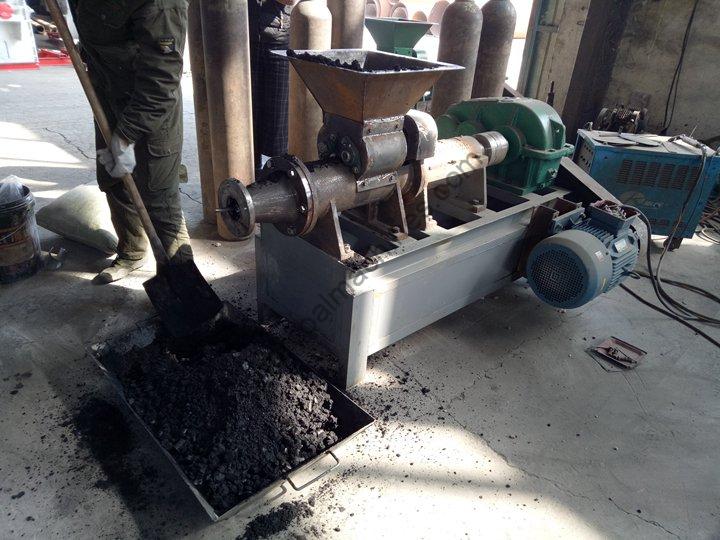
Φυσικά, μπορούμε να χρησιμοποιήσουμε και διαφορετικά καλούπια για να παράγουμε μπρικέτες διαφορετικών σχημάτων. Οι πρώτες ύλες κατάλληλες για την μηχανή εξώθησης άνθρακα είναι συνήθως διάφορες σκόνη ξυλάνθρακα και σκόνη άνθρακα, όπως σκόνη άνθρακα από φλοιό ρυζιού, σκόνη ξυλάνθρακα μπαμπού κ.λπ.
Συντήρηση μηχανής μπρικέτας με κάρβουνο με κέλυφος καρύδας σε χρήση
Όταν χρησιμοποιείτε μηχανή μπρικέτας με κάρβουνο με κέλυφος καρύδας, προσέξτε την αντίστοιχη συντήρηση. Αυτό συμβαίνει επειδή η εύλογη συντήρηση μπορεί όχι μόνο να μειώσει τις βλάβες του μηχανήματος, αλλά και να παρατείνει τη διάρκεια ζωής του μηχανήματος και να εξασφαλίσει τη συνεχή παραγωγή μπρικέτες από άνθρακα καρύδας.
Ως εκ τούτου, για τους περισσότερους κατασκευαστές μπρικέτες ξυλάνθρακα, πρέπει να εκτελείται σωστή συντήρηση προτού ενεργοποιηθεί η μηχανή εξώθησης μπρικετών, κατά τη λειτουργία και μετά τη χρήση. Τα κύρια είδη συντήρησης της μηχανής μπρικέτας με κάρβουνο καρύδας είναι τα εξής:
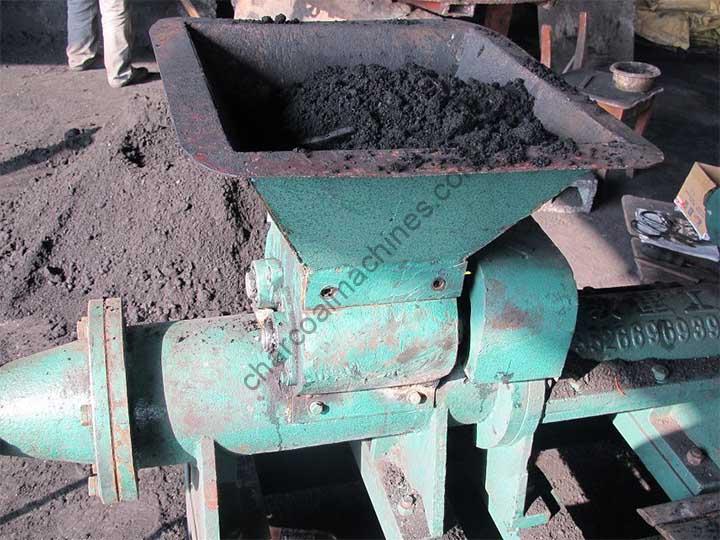
- Πριν χρησιμοποιήσετε τον εξωθητήρα μπρικέτας άνθρακα, ελέγξτε εάν τα περιστρεφόμενα μέρη του είναι εύκαμπτα και εάν υπάρχει μη φυσιολογικός θόρυβος. Αφού το άδειο μηχάνημα λειτουργήσει για 2 έως 3 λεπτά χωρίς ανωμαλία, μπορεί να τεθεί σε παραγωγή.
- Οι πρώτες ύλες πρέπει να έχουν υποστεί προεπεξεργασία και το μέγιστο μέγεθος σωματιδίων της σκόνης άνθρακα πρέπει να είναι μικρότερο από 3 mm. Στη συνέχεια προσθέστε νερό, συνδετικό, σκληρυντικό κ.λπ. Η σκόνη ξυλάνθρακα από κέλυφος καρύδας μπορεί να χρησιμοποιηθεί μετά από ανάδευση για 24 ώρες.
- Εάν το άνοιγμα τροφοδοσίας του μηχανήματος είναι φραγμένο, χρησιμοποιήστε ξύλινες ή μπαμπού λωρίδες για βυθοκόρηση και μην χρησιμοποιείτε ποτέ μεταλλικές ράβδους.
- Τα ρουλεμάν των περιστρεφόμενων μερών της μηχανής θα πρέπει να λιπαίνονται τακτικά. Η θερμοκρασία του φέροντος μέρους της μηχανής Briquette δεν μπορεί να υπερβαίνει τους 60℃.
- Ο μηχανή μπρικέτας με κάρβουνο καρύδας σταματά να τρέφεται πριν σταματήσει την εργασία. Σταματήστε το μηχάνημα αφού το υλικό στον κύλινδρο συμπιεστεί προς τα έξω. Στη συνέχεια, αποσυναρμολογήστε την κεφαλή, καθαρίστε την και τοποθετήστε την ξανά για επόμενη χρήση.
- Προκειμένου να αποφευχθεί η υπερφόρτωση του κινητήρα της μηχανής παραγωγής μπρικετών άνθρακα, συνιστούμε στους χρήστες να εγκαταστήσουν έναν μετρητή ρεύματος και τάσης, ώστε ο χρήστης να μπορεί να προσαρμόσει την ποσότητα τροφοδοσίας σύμφωνα με τα δεδομένα του μετρητή ρεύματος.
Παράγοντες που επηρεάζουν την παραγωγή μπρικέτες άνθρακα καρύδας
1. Συνδετικοί παράγοντες
Όταν λειτουργεί ο εξοπλισμός παραγωγής μπρικέτες καρύδας, η ποιότητα του συνδετικού θα επηρεάσει άμεσα τη σκληρότητα και την πυκνότητα των επεξεργασμένων μπρικετών, καθώς και το κόστος παραγωγής του χρήστη. Ως εκ τούτου, όταν χρησιμοποιείτε εξοπλισμό παραγωγής μπρικέτες άνθρακα καρύδας, είναι απαραίτητο να επιλέξετε ένα κατάλληλο συνδετικό σύμφωνα με τα χαρακτηριστικά του υλικού και την ποιότητα των επεξεργασμένων μπρικετών. Μόνο με αυτόν τον τρόπο μπορεί να διασφαλιστεί η ποιότητα των παραγόμενων μπρικέτες με κάρβουνο καρύδας.

2. Συντελεστής μεγέθους σωματιδίων σε σκόνη άνθρακα
Ο παράγοντας μεγέθους σωματιδίων της σκόνης άνθρακα περιλαμβάνει δύο έννοιες: μέγεθος σωματιδίων και σκληρότητα σκόνης άνθρακα. Είναι οι βασικοί παράγοντες που επηρεάζουν το αποτέλεσμα παραγωγής και την αποδοτικότητα εργασίας του εξοπλισμού παραγωγής μπρικέτες άνθρακα από κέλυφος καρύδας.
Επομένως, πριν η σκόνη ξυλάνθρακα εισέλθει στον εξοπλισμό παραγωγής ράβδων άνθρακα, πρέπει πρώτα να μετρηθεί το μέγεθος των σωματιδίων της. Εάν το μέγεθος των σωματιδίων είναι πολύ μεγάλο, χρησιμοποιήστε εξοπλισμό σύνθλιψης για λεπτή σύνθλιψη. Αφού το μέγεθος σωματιδίων της σκόνης άνθρακα πληροί τις απαιτήσεις, μπορεί να προστεθεί στον εξοπλισμό παραγωγής για παραγωγή.
3. Συντελεστές υγρασίας σκόνης άνθρακα
Όταν το μηχάνημα μπρικέτας με κάρβουνο καρύδας λειτουργεί, εάν η υγρασία του υλικού είναι πολύ υψηλή ή πολύ χαμηλή, θα προκαλέσει το πρόβλημα της πρόσφυσης του υλικού ή τη δυσκολία στο μπρικετοποίηση. Επομένως, είναι απαραίτητο να διασφαλιστεί ότι το υλικό έχει την κατάλληλη υγρασία, όχι πολύ στεγνό ή πολύ υγρό.
Όταν το υλικό είναι πολύ στεγνό, προσθέτουμε νερό και ανακατεύουμε για να αυξηθεί η υγρασία του υλικού. Όταν το υλικό είναι πολύ υγρό, ο εξοπλισμός στεγνώματος μπορεί να χρησιμοποιηθεί για επεξεργασία ξήρανσης. Μόνο όταν η υγρασία των πρώτων υλών είναι λογική, η παραγωγή μπρικέτες άνθρακα μπορεί να εξοικονομήσει χρόνο και προσπάθεια και να βελτιώσει την αποτελεσματικότητα της επεξεργασίας.
Δεν υπάρχουν σχόλια.