Industrial Wood Pellet Machine for Sale
The wood pellet extruder machine is specialized equipment designed for converting raw wood into high-density fuel pellets. This pellet mill is engineered for operational reliability and efficiency, consistently producing uniform pellets.
Industrial Wood Pellet Machine for Sale
The wood pellet extruder machine is specialized equipment designed for converting raw wood into high-density fuel pellets. This pellet mill is engineered for operational reliability and efficiency, consistently producing uniform pellets.
Features at a Glance
Looking for a reliable wood pellet machine to turn biomass waste like sawdust, wood chips, and straw into high-value fuel? As a leading manufacturer, we provide a complete range of wood pellet makers—from small-scale models for home use to heavy-duty industrial wood pellet mills for mass production. Transform your waste into profit and get a custom quote today.
What is a Wood Pellet Machine & How Does It Work?
A wood pellet machine (also known as a wood pellet maker or biomass pelletizer) is engineered to compress low-density biomass materials into high-density, solid fuel pellets. It efficiently processes crops, forest waste, sawdust, and wood chips into a granular fuel with a high specific gravity and hard texture.
The final biomass wood pellets have excellent characteristics: they are easy to ignite, possess a high calorific value, and produce very low ash content after combustion. This makes them a clean, sanitary, and high-quality fuel that can replace coal in industrial and domestic boilers, as well as for civilian cooking and heating.
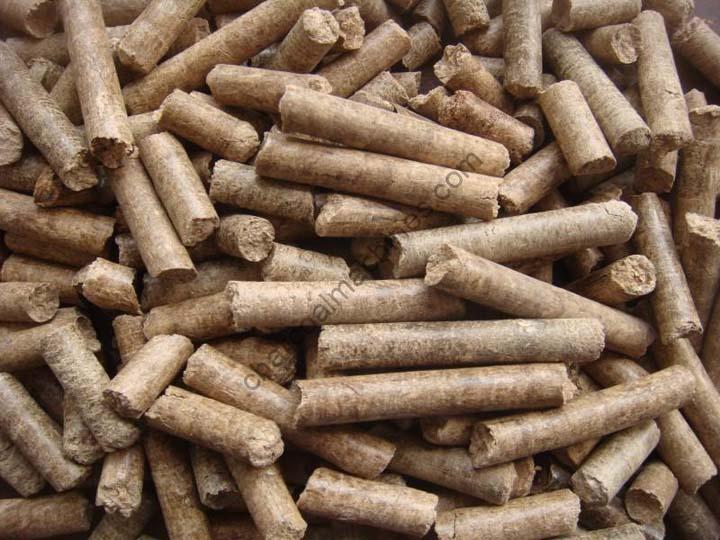
The Working Process
When the wood pellet mill is operating, the process is as follows:
- Feeding: Raw materials (like sawdust from a wood crusher) fall vertically from the feed inlet and are distributed evenly on the surface of the mold by a rotating pressing wheel.
- Pressing & Forming: The material is continuously forced through the holes of the die by the immense pressure of the rollers. During this process, the material is subjected to high pressure and high temperature, causing physical and chemical changes that activate the natural lignin in the wood to act as a binder.
- Cutting & Discharging: A solid, cylindrical body is continuously extruded from the die holes. An internal cutter then slices these cylinders into uniform pellets, which are discharged from the outlet port, completing the pelletizing process.
Watch Our Wood Pellet Extruder Machine in Action
See the entire wood pellet making process from raw material to finished product.
Which Wood Pellet Machine is Right for You? (Models & Applications)
Choosing the right machine depends entirely on your production goals. We offer models for every scale of operation.
1. Small Wood Pellet Machine for Home Use
Ideal for small farms, workshops, or homeowners wanting to produce their own fuel for pellet stoves. These compact wood pellet makers are easy to operate and require minimal space.
- Capacity: 50 – 300 kg/hour
- Best for: DIY fuel production, homemade pellets, small-scale animal feed.
2. Commercial Wood Pellet Machine
Designed for small to medium-sized businesses looking to sell wood pellets locally or for use in commercial boilers. These machines offer an excellent balance of output and investment.
- Capacity: 300 – 800 kg/hour
- Best for: Pellet sales business, large farms, small factories.
3. Industrial Wood Pellet Mill & Production Line
For large-scale manufacturing, our industrial wood pellet mills are the core of a complete wood pellet production line. These robust systems are built for 24/7 operation and high output.
- Capacity: 1 – 5 tons/hour (or more)
- Best for: Mass production for export, biofuel power plants.
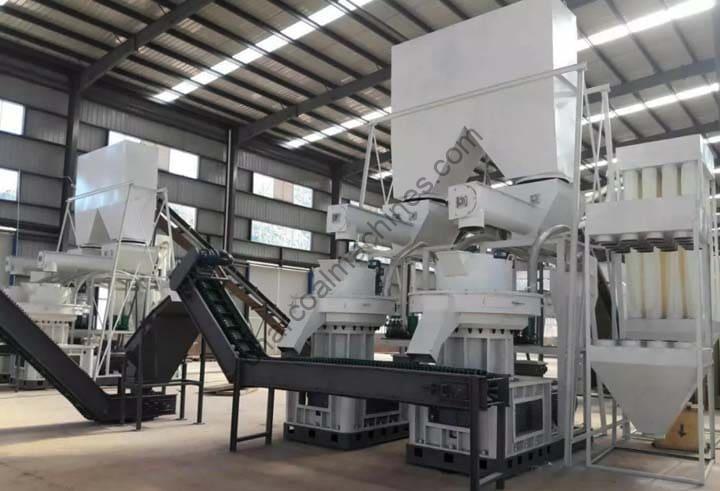
Technical Specifications
Model | Capacity (t/h) | Power (kW) | Pellet Diameter (mm) | Applicable Raw Materials |
---|---|---|---|---|
ZLSP-200 (Small) | 0.1 – 0.2 | 7.5 | 6, 8, 10 | Sawdust, Straw, Rice Husk |
ZLSP-400 (Commercial) | 0.4 – 0.6 | 30 | 6, 8, 10 | Wood Chips, Sawdust, Bark |
MZLH-520 (Industrial) | 1.5 – 2.5 | 132 | 6, 8, 10 | All Biomass, incl. Hardwood |
Note: Specifications are for reference. We offer customized solutions.
Wood Pellet Machine Price
The price of a wood pellet machine can range from $2,000 for a small home-use model to over $100,000 for a complete industrial production line. The final wood pellet machine cost depends on capacity, motor brand, and whether you need ancillary equipment like a crusher, dryer, cooler, and packer. Contact us for a precise, no-obligation quote tailored to your needs.
Main Features & Advantages
- Low Energy Consumption, High Output: With an optimized power supply (e.g., 80KW for a 1-1.5 ton/hr machine), our designs reduce energy consumption by 10-20% compared to similar products, maximizing your profitability.
- Low Labor Cost & High Efficiency: A single set of equipment requires only 2-3 people from production to packaging. The machines are designed for simple operation and maintenance, minimizing downtime.
- Environmentally Friendly Production: The internal design features an integrated dust removal system, ensuring low noise and no smoke or sewage discharge during the production process.
- Durable & Widely Applicable: Our machines have a low wear rate during use and a small footprint, making them suitable for both urban and rural production sites.
- Proven Global Success: We have successfully installed over 500 pellet lines in 30+ countries, including Canada, the USA, and Malaysia.
Detailed Machine Structure
Our vertical wood pellet machine has a compact structure and beautiful appearance, making it easy to move on the working site. It is composed of a pellet machine base, a large reduction gearbox, a bearing room, a feeding hood, a discharging part, a motor, a pressure roller assembly, and a mold. The electric motor is connected directly to the reducer shaft. After a 90° change of direction, the motor drives a vertical spindle, which in turn drives the roller to roll along the inner surface of the mold to complete the pressing process.
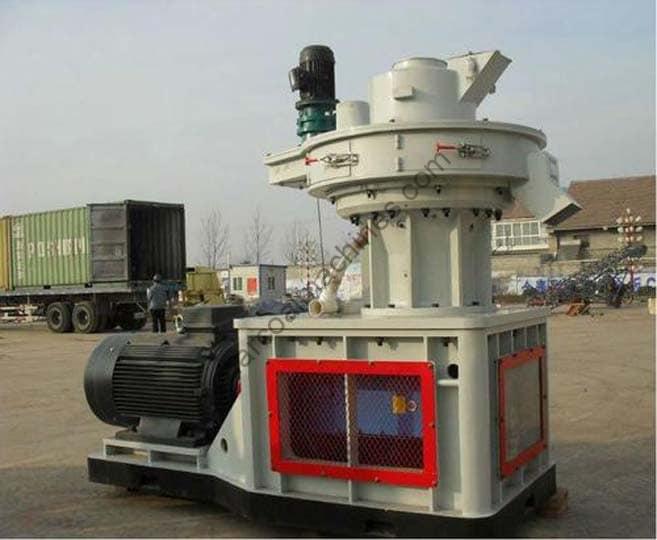
Wood Pellet Machine Maintenance Tips
- During production, grease the pressure roller every 2 hours using a manual roller at the main shaft end.
- Before each work session, fill the auger and agitating bearing with No. 2 lubricant.
- Fill the machine’s stirring reducer with molybdenum disulfide lithium-based grease every six months.
- The bearings of the auger and agitator shafts should be cleaned and have their oil changed every two years.
- For long-term storage, press oily, non-deteriorating materials through the machine to fill the mold holes. Clean all parts of material residue and cover the machine with a plastic cover.
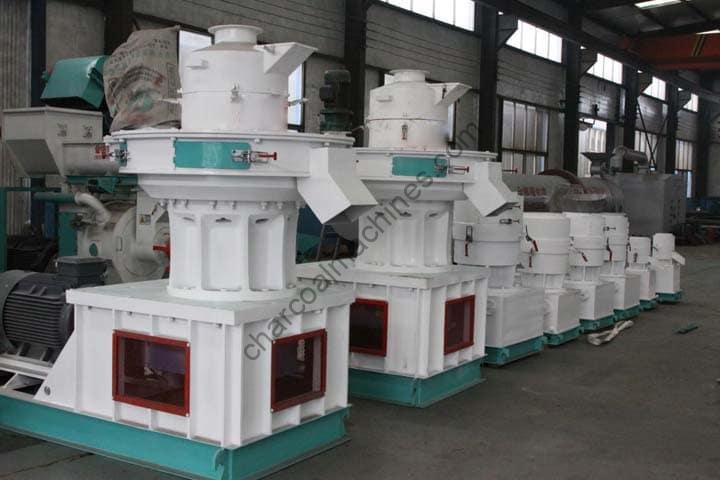
Frequently Asked Questions (FAQ)
What raw materials can be used?
Our machines can process a vast range of biomass, including sawdust, wood shavings, wood chips, straw, rice husks, peanut shells, and more. The ideal moisture content is 12-18%.
How much is a wood pellet making machine?
As mentioned, prices vary greatly. A small machine starts around $2,000, while industrial lines are a significant investment. Contact us with your raw material and capacity requirements for an accurate price.
Do you have wood pellet machines for sale in Canada?
Yes, we ship worldwide, including to Canada. We have several clients in British Columbia and Ontario and can handle all logistics and customs clearance for your order.
What is the complete wood pellet making process?
A full production line typically includes: Chipping/Crushing → Drying → Pelletizing → Cooling → Sieving → Packaging.
Ready to Start Your Pellet Business?
Our experts are ready to help you choose the perfect machine and provide a detailed quotation. Contact us via online chat or email to get started on your project!
Hot Product
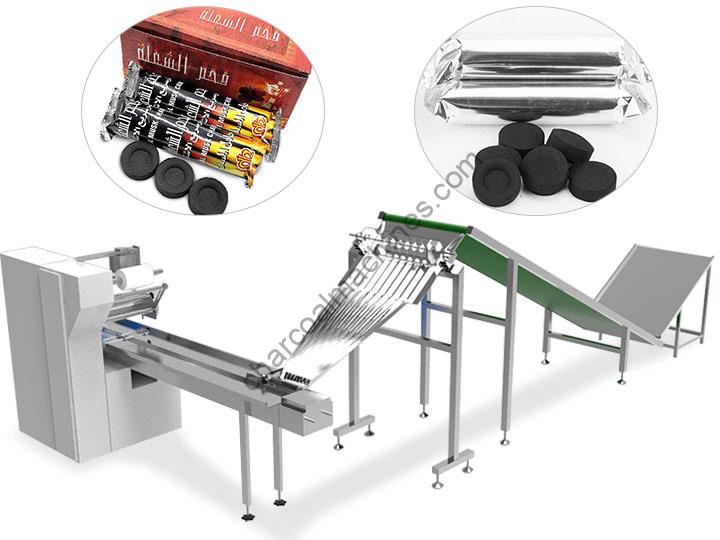
Shisha (Hookah) Charcoal Production Line | Briquette Packaging Dryer Plant
The automatic shisha(hookah) charcoal production line is the…
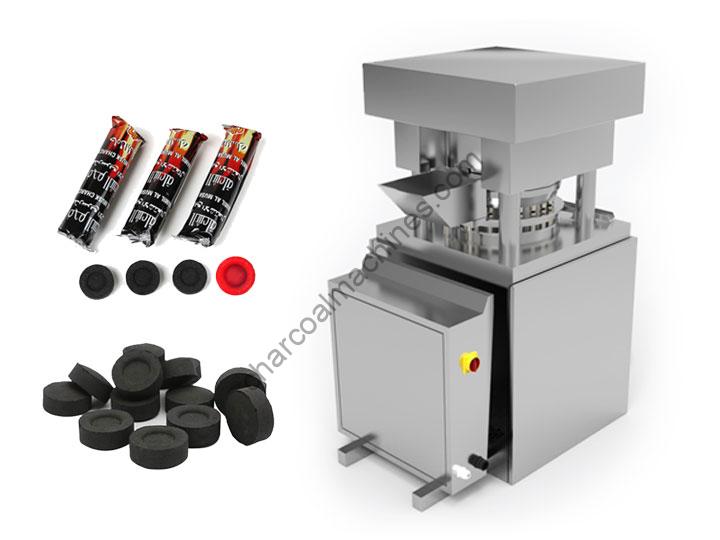
Hookah Charcoal Machine to Make Round & Cube Shisha Charcoal
Shuliy shisha charcoal press machine is designed according to…
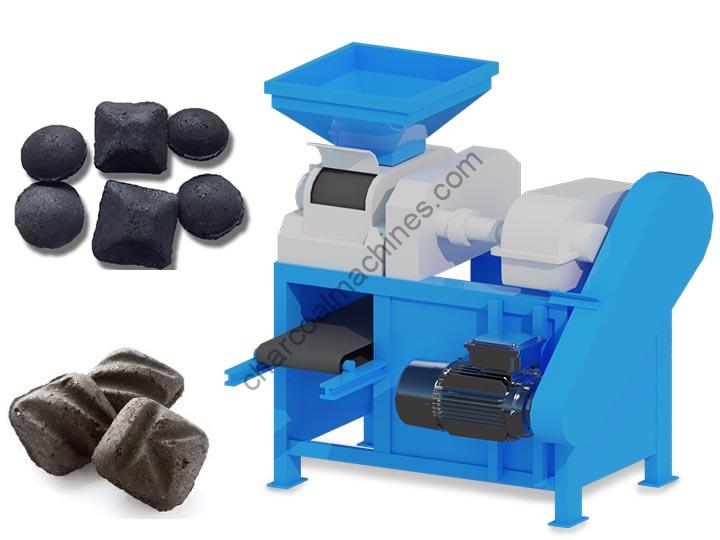
Round & Pillow Barbecue Charcoal Ball Press Machine
Barbecue charcoal press machine can make compressed charcoal…
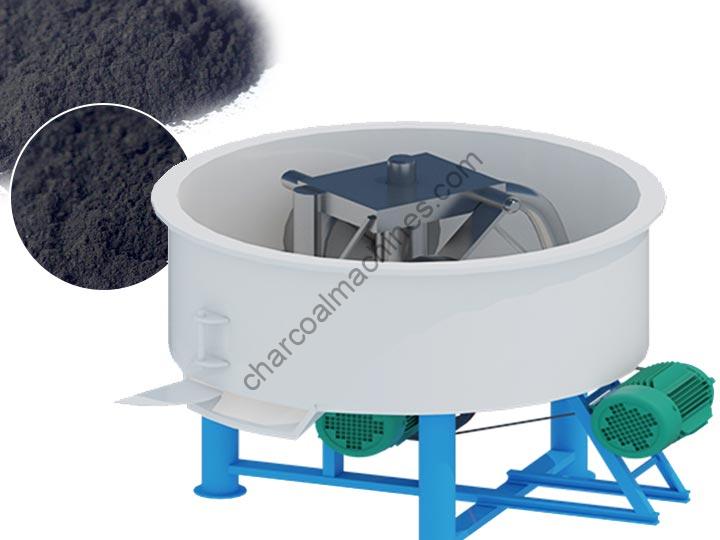
Charcoal Grinder Machine for Making Fine Charcoal Powder
The lump charcoal grinder machine also known as…
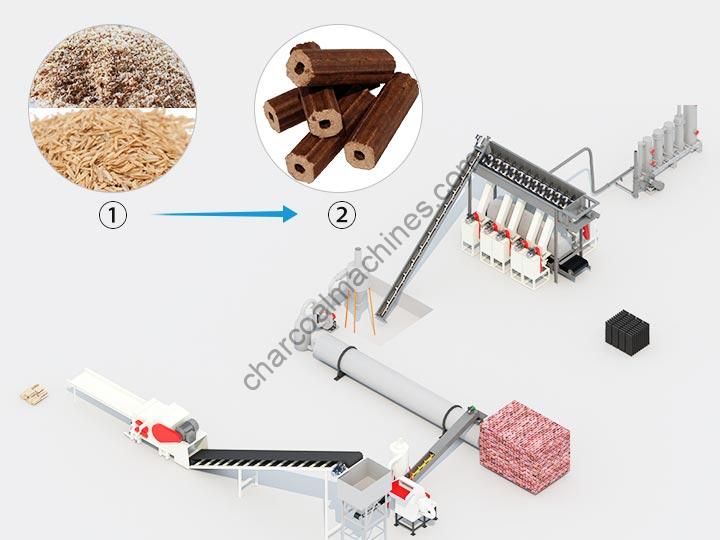
Wood Sawdust Briquettes Production Line | Pini Kay Heat Logs Plant
The wood sawdust briquettes production line mainly extrudes…
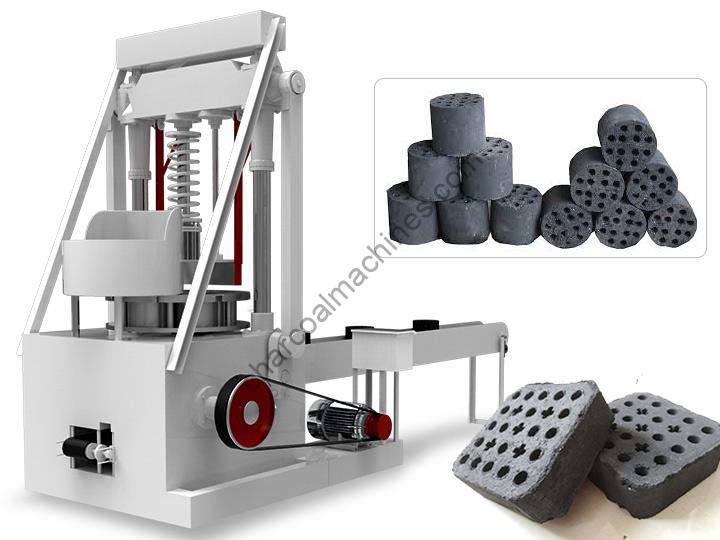
Honeycomb Coal Briquette Press Machine
The honeycomb coal briquette machine can press the pulverized charcoal powder…
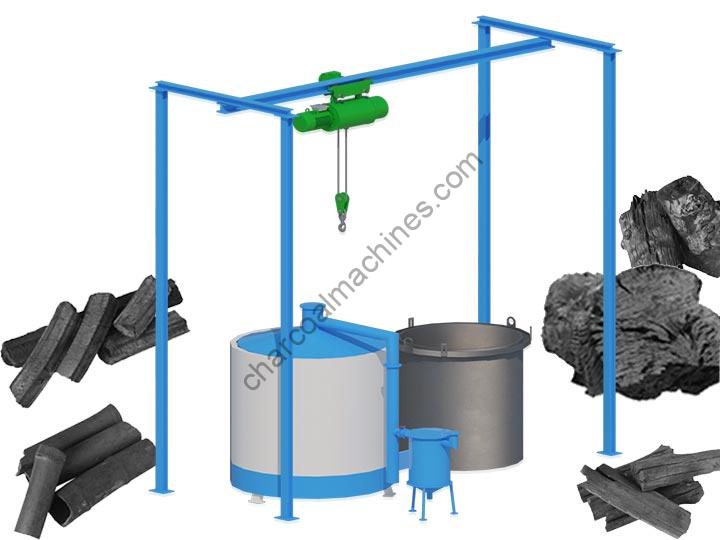
Vertical Carbonization Furnace For hardwood Charcoal Production
The airflow hoisting carbonization furnace is currently the…
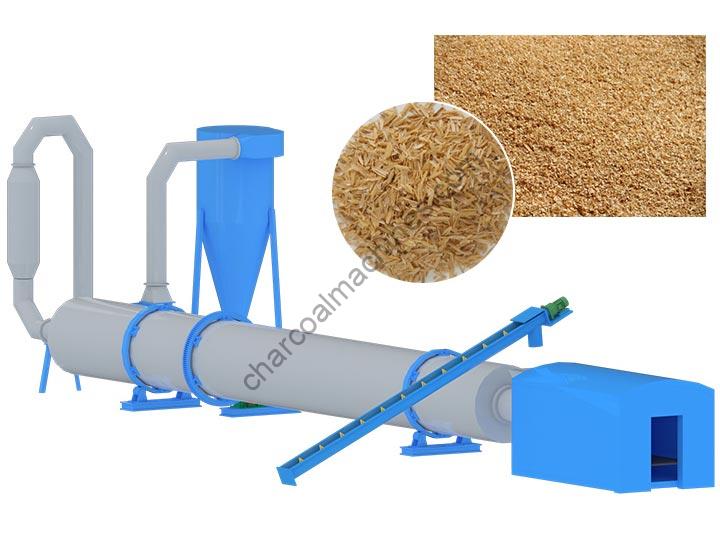
Continuous Dryer for Drying Sawdust & Rice Husk
Industrial sawdust dryers and rice husk drying machines…
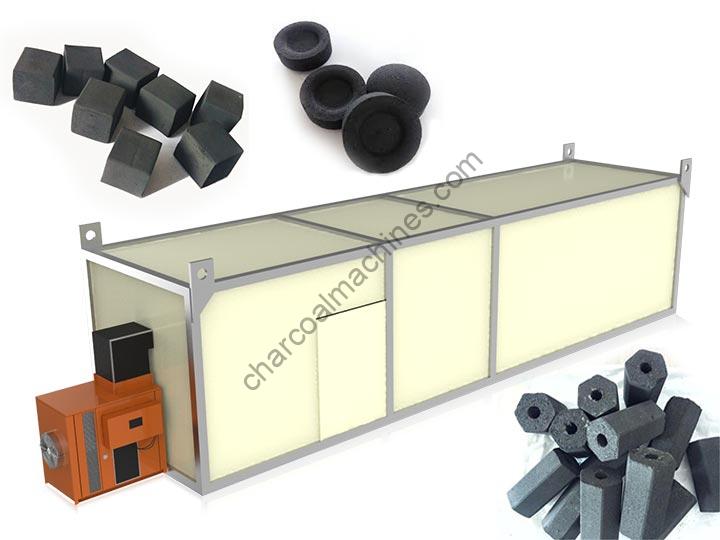
Batch Charcoal Drying Machine with Good Performance
The charcoal dryer machine is mainly used to…
2 comments