Charcoal Machine & Production Line for Making BioCharcoal
Charcoal making machine, also known as charcoal production line, consists of several machines. First, the raw materials are pulverized into sawdust with a diameter of less than 5mm using a wood crusher. Then, the sawdust is dried using a rotary type of sawdust dryer to reduce moisture. Next, the material is shaped using a briquette machine. Finally, it is placed in a carbonization furnace for carbonization.
This series of biomass carbonizing machines can process wood branches, sawdust, rice husk, coconut shells, straw, bamboo, plan kernel shells, and other waste biomass materials into charcoal. And the charcoal products can be hookah or shisha charcoal, barbecue charcoal, honeycomb coal, and various types of charcoal briquettes.
Shuliy factory makes and sells biomass charcoal machines. They can customize charcoal plants and offer processing solutions to customers at good prices, both in and outside the country.
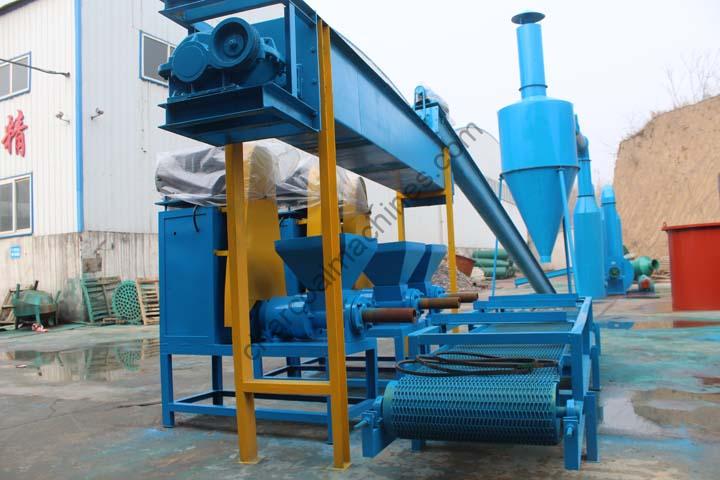
How to make charcoal in a commercial?
Industrial charcoal processing equipment is essential for the modernization of charcoal production. Various charcoal production lines and processing solutions have boosted efficiency for many processors and generated significant benefits.
The charcoal production line is a general term for a series of charcoal and coal processing equipment. We can produce various types of charcoal by adjusting the performance and setup of charcoal making machines. These types include natural charcoal, lump charcoal, round shisha charcoal, cube hookah coal, barbecue charcoal, honeycomb coal, and hexagonal charcoal.
Definition of charcoal machines
Charcoal machines usually include single charcoal machines and complete processing lines. Regardless of the scale of charcoal plants opened by charcoal processors, they usually need to use a certain number of charcoal machines to complete the production.
For example, sawdust making machine, sawdust dryer, pini kay briquette machine, lump charcoal powder grinder, charcoal & coal briquettes forming machine, coal & charcoal briquettes dryer machine, etc. They all play an important role in the process of charcoal production.
Charcoal briquettes making production line supplier
Charcoal briquettes are the ideal material for heating in winter, it can also be used in a variety of restaurants and steel equipment factory production.
Charcoal machine production line is a variety of charcoal equipment combination of short. The main equipment of the charcoal machine production line includes a crusher, dryer, briquette machine, and carbonization furnace.
The raw materials for making charcoal can be sawdust, rice husk, fruit shell, straw, logs, branches, scraps, and other biomass materials. The humidity of the raw material should be less than 12%. The production area of the charcoal making machine production line needs to be more than 50 square meters, the height needs to be more than 4 meters.
Raw materials for making charcoal
Natural lump charcoal: all kinds of woodblocks, log sections, small branches, and straw. Such as oak, hardwoods, beech, pine, elm, bamboo, cotton stalk, etc. Many agricultural and forestry wastes, such as straw, corn stalks, peanut husks, corn cobs, rice husks, palm kernel shells, coconut husks, etc. can also be used as raw materials for charcoal processing.
Shisha & hookah charcoal: coconut shell and fruit trees are the best raw materials.
Barbecue charcoal: rice husks, hardwoods, coconut shells, etc.
Production principle of charcoal making machine
The type of wood crusher can be selected according to the raw material size and humidity to be carbonized. The dryer and the sawdust briquette machine, are the dedicated machinery to produce machine-made charcoal. The dryer can be divided into airflow dryer machines and rotary dryer machines according to the raw material, dry humidity, and production requirements.
These two kinds of dryers have the advantages of automatic feeding, the smoke outlet is not channeling material, the outlet is not spraying material. The briquette machine capable of automatically controlling temperature can adjust the compactness of the biomass rods at any time to further ensure the quality of the rods. The charcoal produced by charcoal machine production equipment is of big density, small size, good flammability, can replace firewood and coal burning.

Features of complete charcoal processing plant
- The whole charcoal production process of the charcoal machine production line has been done airtight and dustproof treatment, will not cause smoke and dust pollution to the environment, can ensure a good working environment and effectively protect the ecological environment, which can also promote the environmental protection and energy saving of charcoal production.
- Charcoal processing line can realize the machine-made charcoal assembly-line production, save labor, and reduce labor intensity, greatly improve the production efficiency of charcoal, also further improve the production capacity, improve economic benefits for manufacturers.
- The combination of the whole set of charcoal making machine for sale can be comprehensively equipped and assembled according to the material types, size, and dry humidity of the raw materials, as well as the production needs and output requirements of customers. It is easy and flexible to meet the needs of different customers to the greatest extent.
Basic output type of charcoal processing plant
Basic output charcoal making machine is a variety of charcoal equipment combination of short. The main equipment of the charcoal briquettes production line includes the crusher, dryer, briquette machine, and carbonization furnace.
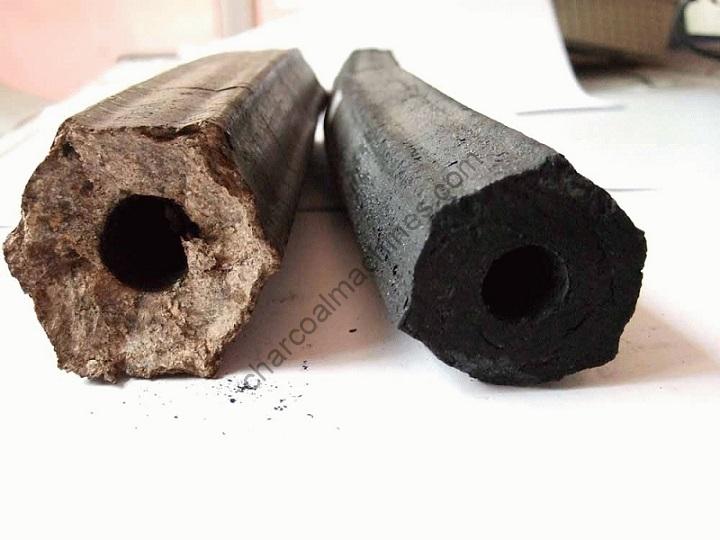
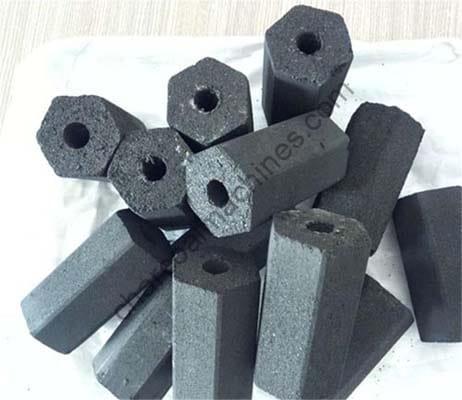
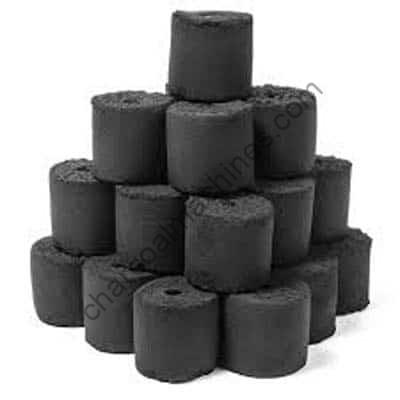
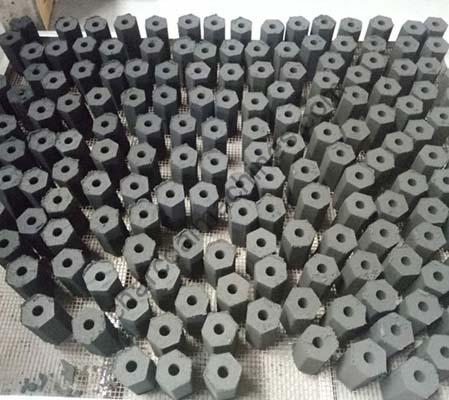
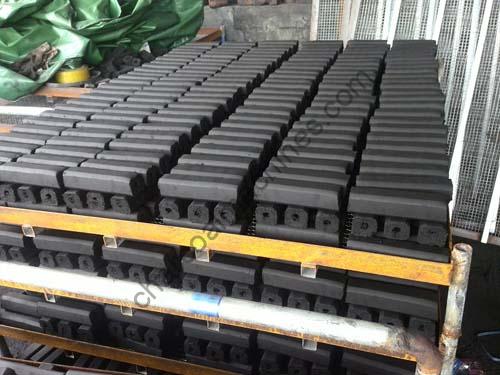
The machine-made charcoal produced by the charcoal production line gradually replace people’s original kiln burning charcoal, let people’s production costs greatly reduced, production profits greatly double. The charcoal processing plant is a variety of charcoal equipment combination of short. The main equipment of the Charcoal production line includes a crusher, dryer, sawdust briquette machine, and carbonization furnace. Charcoal production lines of raw materials can be sawdust, rice husk, fruit shell, straw, logs, branches, scraps, and other materials. The humidity of the raw material should be less than 12%. The production area of the Charcoal production line needs to be more than 50 square meters, the height needs to be more than 4 meters.
1 Crusher
Production principle of the biomass charcoal making machine
The charcoal production line is a series of machines that mainly go through the sawdust crusher to pulverize the raw materials into 10mm particles, after drying by the dryer, and then use the sawdust briquette machine to shape the material, and then put into the carbonization furnace for carbonization.
The type of crusher can be selected according to the raw material size and humidity to be carbonized.
The dryer and the sawdust briquette machine, are the dedicated machinery to produce machine-made charcoal. The dryer can be divided into airflow dryer machines and rotary dryer machines according to the raw material, dry humidity, and production requirements.
These two kinds of dryers have the advantages of automatic feeding, the smoke outlet is not channeling material, the outlet is not spraying material. The sawdust briquette machine capable of automatically controlling temperature can adjust the compactness of the rod at any time to further ensure the quality of the rod.
The charcoal produced by the Charcoal processing line is of big density, small size, good flammability, can replace firewood and coal burning.
Features of Wood Charcoal Making Machine
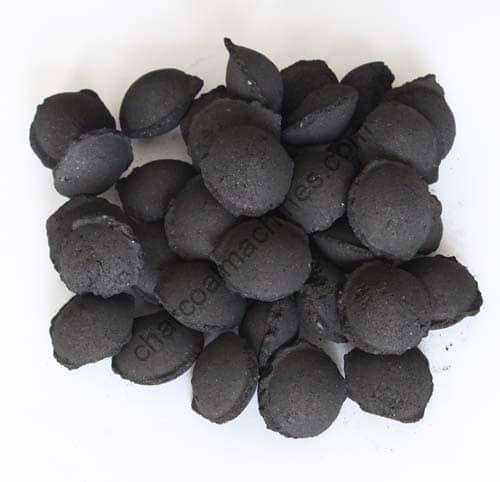
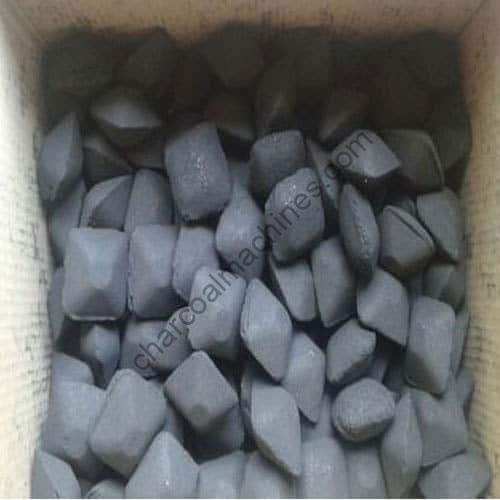
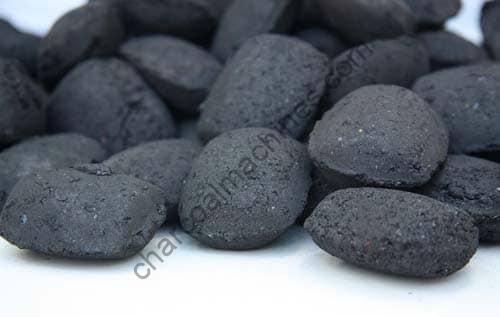
- The whole production process of the wood charcoal line has been done airtight and dustproof treatment, will not cause smoke and dust pollution to the environment, can ensure a good working environment and effectively protect the ecological environment, which can also promote the environmental protection and energy saving of charcoal production.
- The charcoal production line can realize the machine-made charcoal assembly-line production, save labor and reduce labor intensity, greatly improve the production efficiency of charcoal, also further improve the production capacity, improve economic benefits for manufacturers.
- The combination of the whole set of charcoal making machine equipment can be comprehensively equipped and assembled according to the material types, size, and dry humidity of the raw materials, as well as the production needs and output requirements of customers. It is easy and flexible to meet the needs of different customers to the greatest extent. According to the production requirements of customers, a reasonable allocation of the charcoal production line can be customized.
Charcoal machines detail PDF download
The full-automatic charcoal production plant
Charcoal making machine can turn waste into treasure, make full use of all available agricultural and forest resources, through the sawdust briquette machine’s high temperature and high pressure made into the machine-made rod, and then the machine-made bar is transformed into smokeless, tasteless, and non-toxic machine-made charcoal rod by the equipment of the carbonizing furnace.
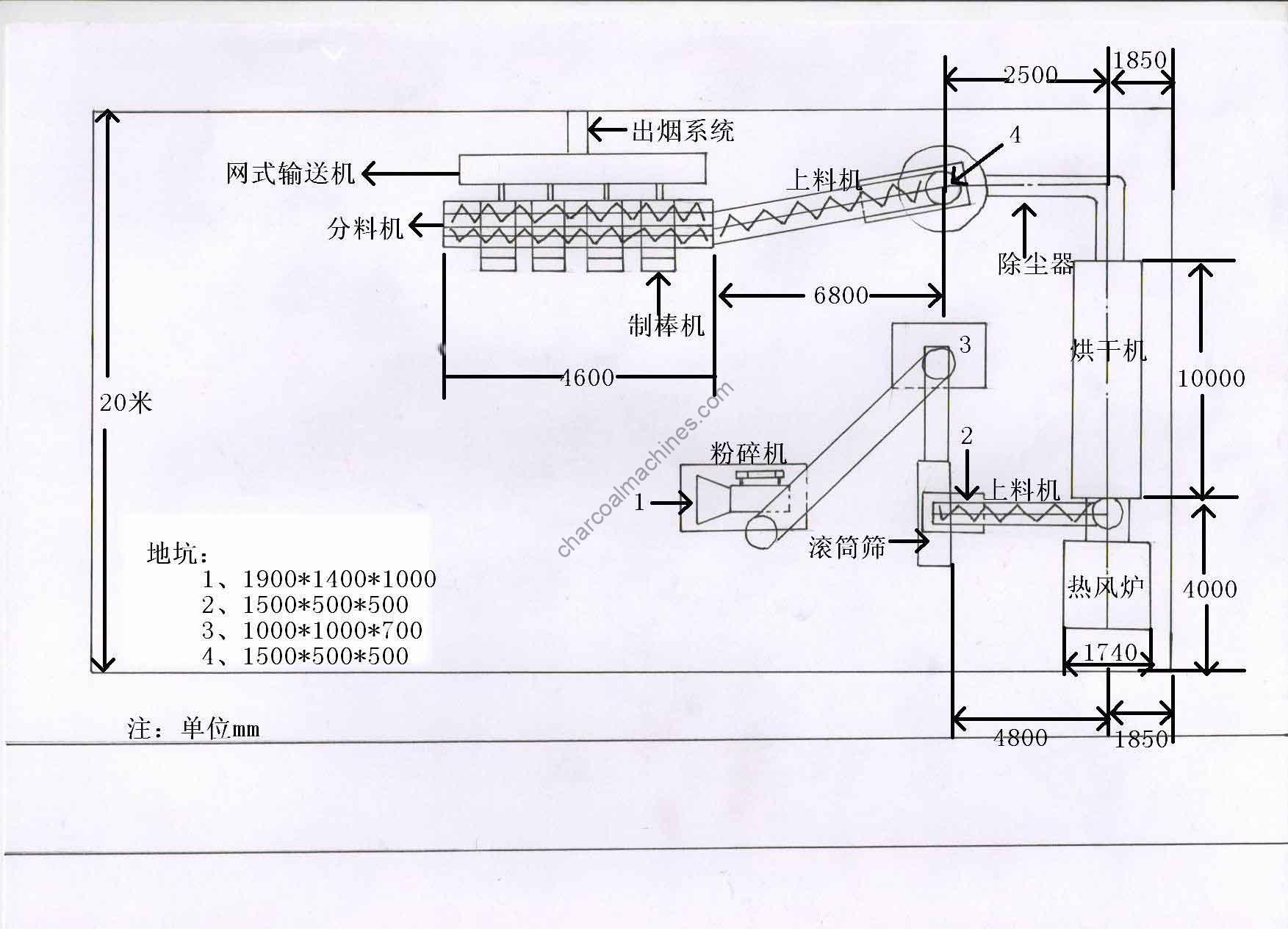
The automatic charcoal briquettes production process
Machine-made charcoal is widely used in agriculture, industry, environmental protection, smelting, civil life, and other categories. With people’s increasing demand for charcoal, the automatic charcoal production line which can be used for efficient production is becoming more and more popular.
The automatic charcoal production line as the name implies is in a person’s operation can be put into production, completely effortless, can save a lot of labor and production costs.
General charcoal machine production line comprises a series of basic charcoal making equipment such as crusher, dryer, sawdust briquette machine, and carbonization furnace. Such a production line often needs at least 3-5 people for charcoal production.
Based on the original equipment, the automatic charcoal making line added some special equipment such as screw feeder, rotary screen, distributor, and net belt conveyor, fully realized automatic production of charcoal.
Two types of charcoal production processes
- Molding before carbonization: raw materials — crushing, screening — drying — rod making — carbonization — packaging. Sawdust, wood chips, cotton stalk, rice husk, and other raw materials after crushing by the crusher will be conveyed by screw feeder into airflow dryer machine or rotary dryer machine(corresponding dryers can be chosen according to the dry humidity of raw materials and production needs ) for drying. After drying, the materials are transported from the screw feeder to the distributor. The distributor can distribute the raw materials evenly to be placed in the lower sawdust briquette machine (in the production line, according to the production demand, more than one sawdust briquette machine can be set). The hollow rod formed by the sawdust briquette machine is exported by the net belt conveyor. Workers collect and sort these hollow rods from the conveyor, and then send them to the carbonization furnace to be carbonized into finished carbon rods.
- Carbonization before molding: raw material — carbonization — mixing and milling (water and additive) — molding — air drying and warehousing. Walnut shells, chestnut shells, cotton stalk, corn stalk, and other raw materials are first carbonized by the carbonizing furnace (the carbonization furnace shall be selected according to the raw materials to be carbonized). The charcoal after carbonization should be crushed by a charcoal crusher (the corresponding crusher can be selected according to the crushing degree of charcoal). After the charcoal is crushed into powder, it should be added with water and adhesive and mixed evenly by a grinding blender. After that, it is pressed by the charcoal briquette machine to form the final finished charcoal briquettes like charcoal rods, hookah charcoal briquettes, charcoal ball, honeycomb charcoal, and BBQ charcoal, which can be packaged and stored in the warehouse or sold after being dried by the drying box.
Features of the automatic charcoal making machines
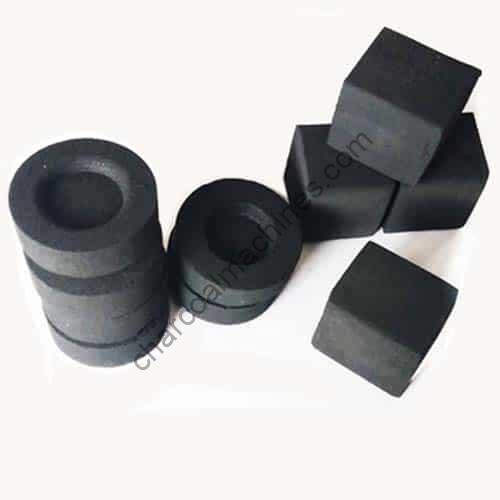
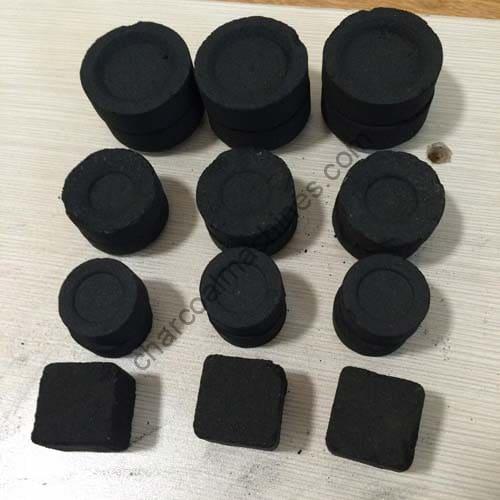
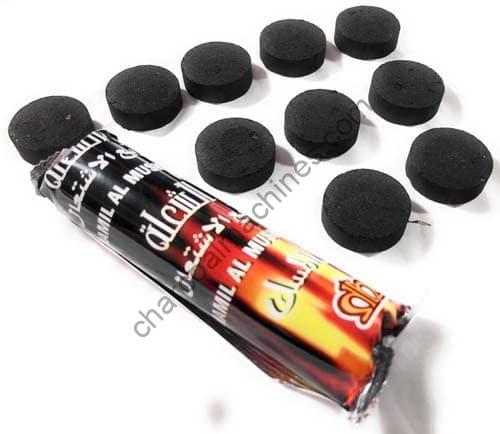
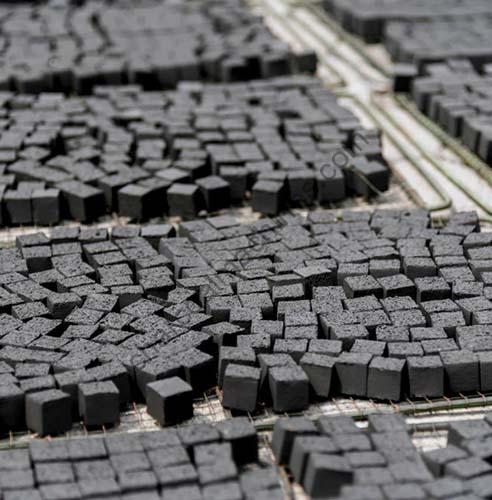
- The automatic biomass charcoal production line has a high degree of automation, which can reduce the original single machine operation from 5-8 people to 1-2 people, greatly reduce the input of human and material resources, increase output and expand economic benefits.
- The raw materials of the complete set of charcoal machines are wide and in low price, all kinds of raw materials can be used with the corresponding charcoal machine production line, and the shape of the charcoal produced is regular, with carbon content up to 75-85%, high heating value and long burning time.
- The operation cost of the whole equipment is low, the raw material crushing rate is high, energy-saving, and environmental protection, the output is big, and the pollution is little.
- Compared with other product lines, the operation and maintenance of this whole set of charcoal making equipment are very simple, wearing parts with the latest domestic high-strength and wear-resisting materials, small loss and long service life can bring customers considerable economic benefits. According to the actual production requirements of customers, a reasonable allocation of automatic charcoal machine production lines can be customized by our professional charcoal machine technicians.
Output: according to raw materials and production requirements, we can customize the appropriate charcoal production lines.
Why is the charcoal business soaring these years?
In recent years, the development of the environmental protection industry is more and more rapid, environmental-friendly charcoal production industry has gradually caused social attention, machine-made charcoal is also more and more favored by the majority of market users.
The increased demand for machine-made charcoal makes the charcoal machine equipment and charcoal production process of the charcoal making machine for sale constantly innovative development. Charcoal production line which can produce medium-output and high-quality machine-made charcoal has become an urgent demand in the market.
Charcoal production line according to the raw material and production demand can be very flexibly collocated. Shuliy machinery can also provide customers with a reasonable and efficient charcoal production line equipment scheme free of charge according to the requirements of customers.
Shuliy machinery based on many years of charcoal machine production and sales experience and reasonable adoption of many customers from different countries use experience and feedback suggestions, sorted out the basic medium charcoal production line for customers’ reference and selection.
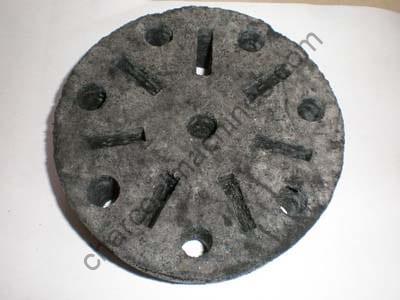
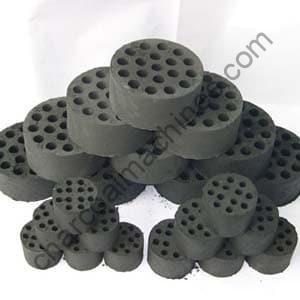
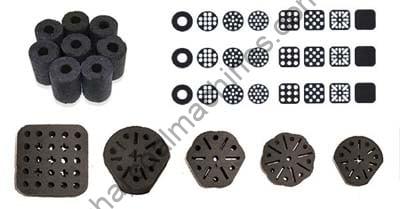
Comprehensive classification of charcoal production lines
According to different raw materials, production conditions, and different charcoal processing techniques, the charcoal production line configuration we use is different.
At present, the most conventional charcoal processing technology is mainly divided into two types: 1. Sawdust briquettes making first, then carbonizing. 2. Raw materials carbonizing first, then briquetting. Based on the current charcoal production process, our factory has designed the following charcoal production lines that are most popular in the market.
Sawdust charcoal production line | Pini kay charcoal & coal plant
The main production links of this automatic sawdust charcoal processing line include wood crushing, sawdust drying, sawdust briquettes extruding, sawdust briquettes carbonizing(pini-coal making).
Raw materials: logs, wood scraps, branches.
Sawdust requirements: the best size is between 3-5mm. The moisture content after drying should be less than 12%.
Final product: pini kay briquettes, sawdust charcoal briquettes, pini-coal
Features: the sawdust briquette shapes can be customized.
At present, this sawdust charcoal production line is very popular with investors and processors from most African countries, the Middle East, Southeast Asia, and a small number of European countries.
Our factory designed sawdust charcoal production lines with output of 2-3t/d, 4-5t/d, and 8-10t/d according to the needs of many domestic and foreign customers. The main factors affecting the output of charcoal are the configuration of the production line and the choice of the machine model.
2-3 ton per day sawdust charcoal processing project
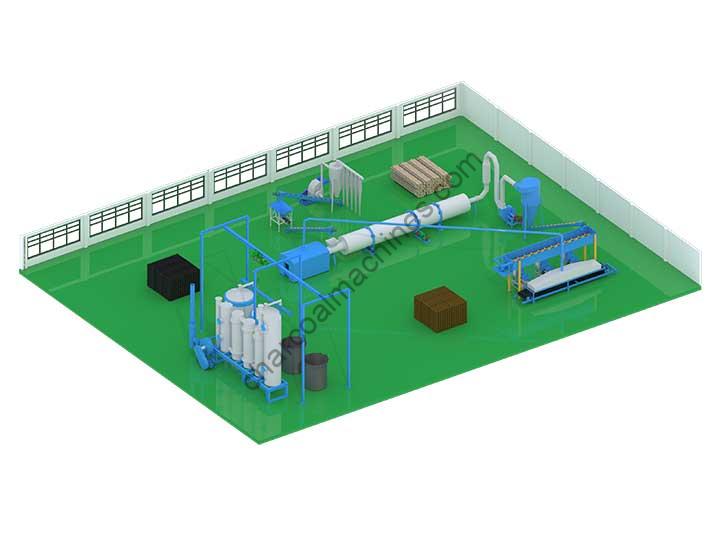
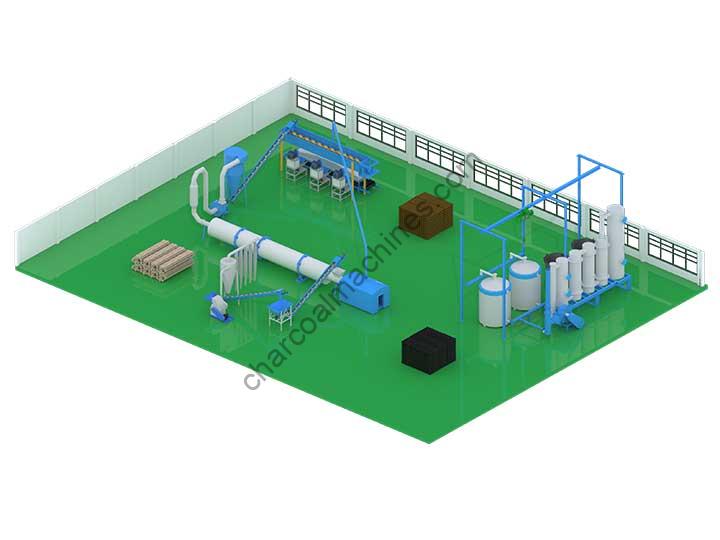
Configuration list of 2-3t/d sawdust briquette charcoal plant design
No. | Item | Specification |
1 | Wood crusher | Model: SL-60 Power:22kw Capacity:800-1000kg per hour |
2 | Screw conveyor | Power:2.2kwLength:4m |
3 | Rotary dryer | Model: SL-R1000 Power:7.5+7.5kw Capacity:800-1000kg per hour Dimension: φ1*10m |
4 | Screw convey | Power:2.2kw Length:4m |
5 | Distributor | Dimension:4.5*1.05*2.1m Power:4kw |
6 | Sawdust briquette machine | Model: SL-B50 Power:18.5kw Capacity:250kg per hour |
7 | Mesh conveyor | Length:6m |
8 | Carbonization furnace | Model: SL-C1500 Dimension:2.2*2.2*2m Capacity:2-3t per day, including 3 inner stoves |
4-5 ton per day sawdust charcoal processing project
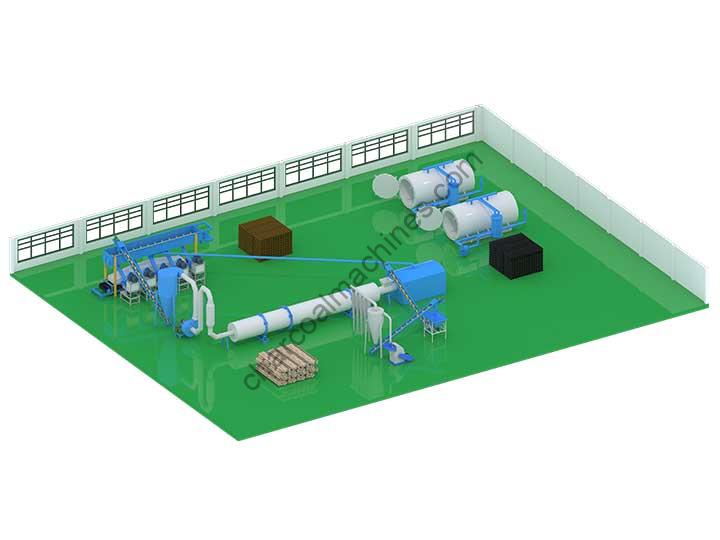
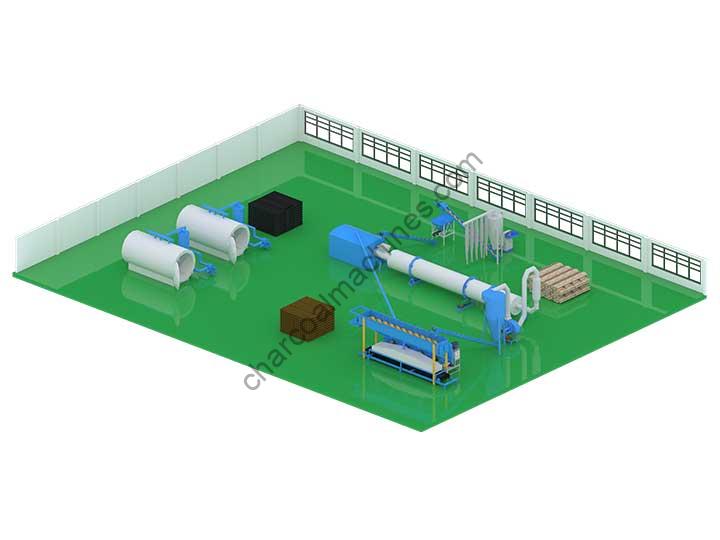
Configuration list of 4-5t/d sawdust briquette charcoal plant design
No. | Item | Specification |
1 | Wood crusher | Model: SL-80 Power:37+7.5kw Capacity:1500-2000kg per hour |
2 | Screw conveyor | Power:2.2kw Length:4m |
3 | Rotary dryer | Model: SL-R1000 Power:7.5+7.5kw Capacity:800-1000kg per hour Dimension:φ1*10m |
4 | Screw conveyor | Power:2.2kw Length:4m |
5 | Distributor | Dimension:6.4*1.05*2.1m Power:4kw |
6 | Sawdust briquette machine | Model: SL-B50 Power:18.5kw Capacity:250kg per hour |
7 | Mesh conveyor | Length:7m |
8 | Carbonization furnace(3 sets) | Model: SL-C1500 Dimension:4.5*1.9*2.3m Capacity:4-5t per day, horizontal furnace |
8-10 ton per day sawdust charcoal processing project
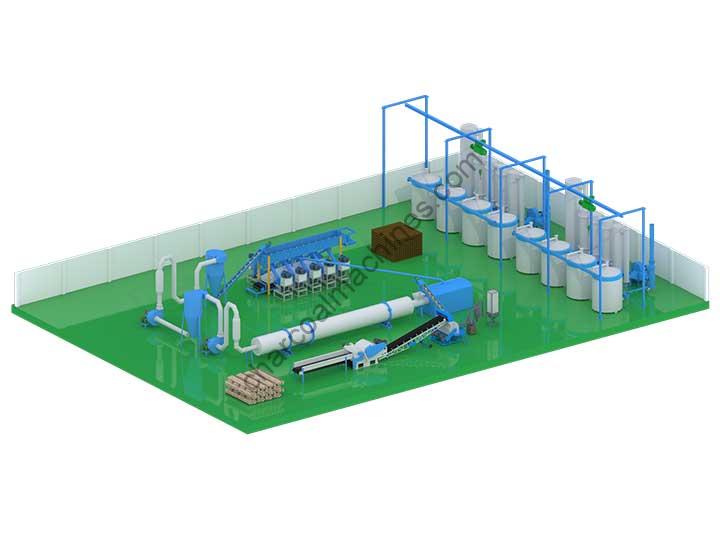
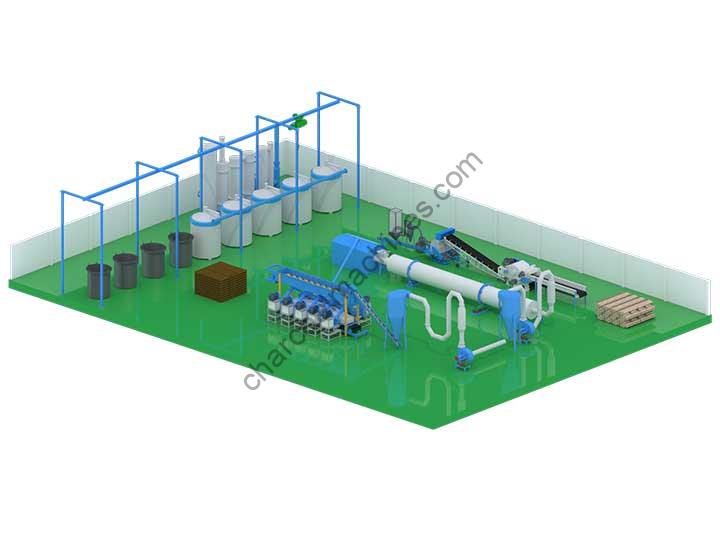
Configuration list of 8-10t/d sawdust briquette charcoal plant design
No. | Item | Specification |
1 | Belt conveyor | Length:6m Width:50cm Power:3kw |
2 | Wood crusher | Model: SL-80 Power:37+7.5kw Capacity:1500-2000kg per hour |
3 | Screw conveyor | Power:2.2kw Length:4m |
4 | Storage bin | Size: 1.5*1.5m Storage: about 2t Power:1.5kw |
5 | Screw conveyor | Power:2.2kw Length:4m |
6 | Rotary dryer | Model: SL-R1000 Power:7.5+7.5kw Capacity:800-1000kg per Dimension:φ1*10m |
7 | Screw conveyor | Power:4kw Length:6m |
8 | Distributor | Dimension:6.4*1.05*2.1m Power:4kw |
9 | Sawdust briquette machine(10 sets) | Model: SL-B50 Power:18.5kw Capacity:250kg per hour |
10 | Mesh conveyor | Length:7m |
11 | Carbonization furnace(8sets) | Model: SL-C1500 Dimension2.2*2.2*2m Capacity:8-10t per day, including 8 sets furnace |
Complete charcoal production line video
Briquettes processing plant for shisha charcoal, barbecue charcoal, honeycomb coal
The process of charcoal briquettes plant generally starts with the carbonization of raw materials. Then, the charred coconut shell charcoal and rice husk charcoal will be crushed and stirred (with a certain proportion of binder) to make briquettes.
And we will use different charcoal briquettes molding machines to press the carbon powder into different shapes and sizes. The charcoal briquettes production line usually includes a continuous carbonization furnace, charcoal crusher, wheel grinder mixer, briquettes extruder, briquettes dryer, etc.
Regular charcoal briquettes production line
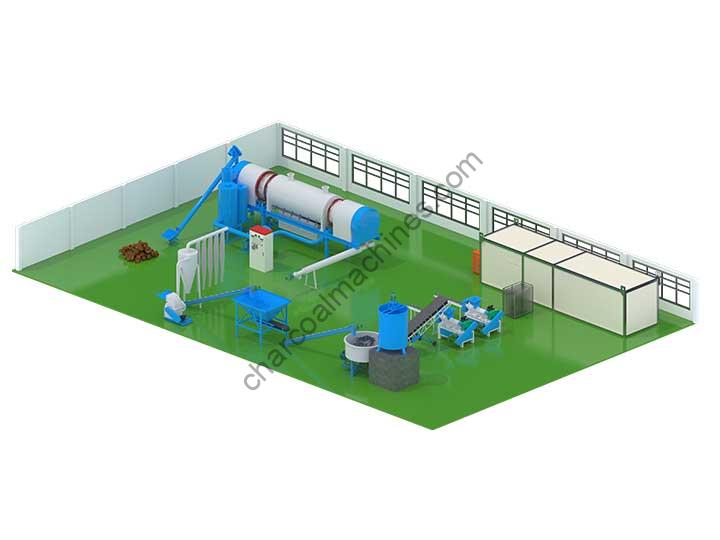
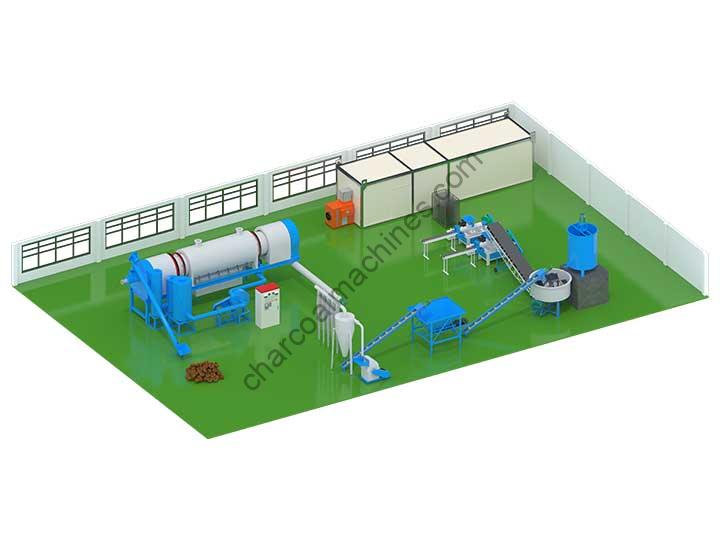
Note: the main equipment in this project is the briquettes extruder machine. By changing with different extruding molds, we can customize the briquettes’ shapes. Besides, we always match the charcoal extruder with charcoal cutting devices to determine the briquettes’ sizes and lengths.
Charcoal briquettes processing plant video
Shisha & hookah charcoal production line
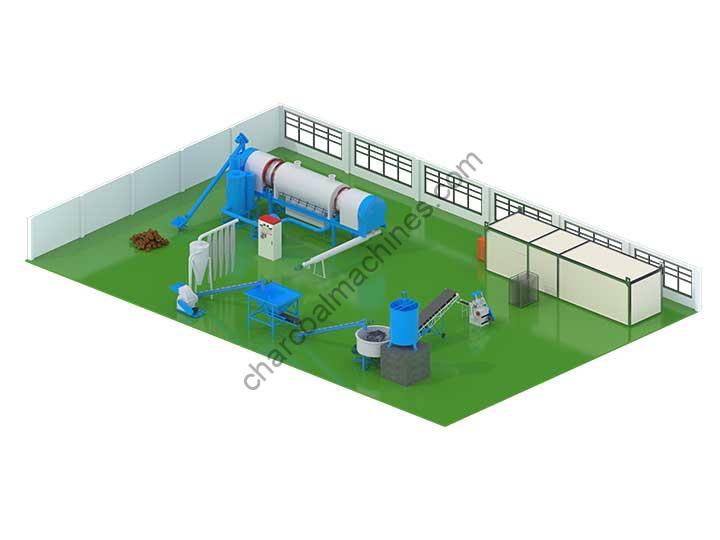
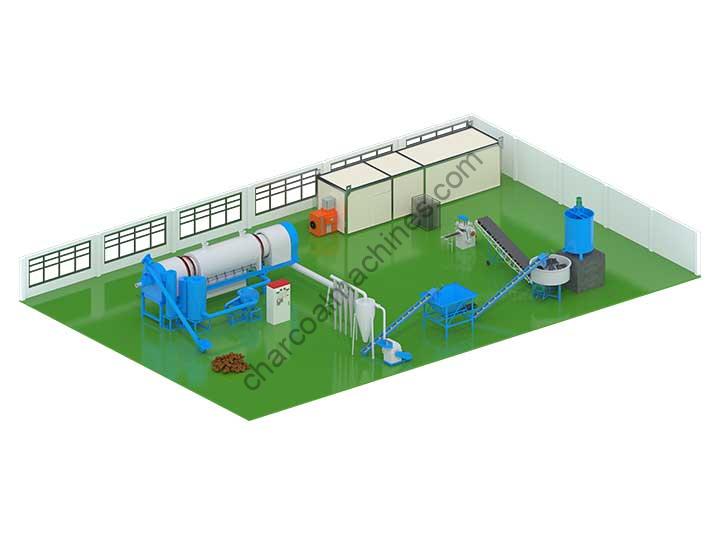
Note: the shisha charcoal press machine is very important for this plant, which can determine the specifications of the hookah charcoal you made. Its press molds can also be exchanged to make both cube and round shisha charcoal. The common size of square shisha charcoal is 20*20mm, 25*25mm. And the round hookah coal is 30mm, 33mm, 35mm, 40mm.
Hookah charcoal processing plant video
Barbecue charcoal production line
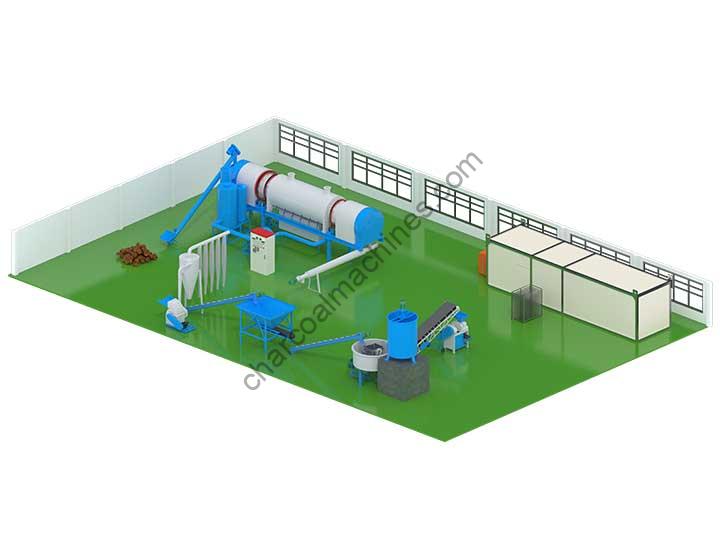
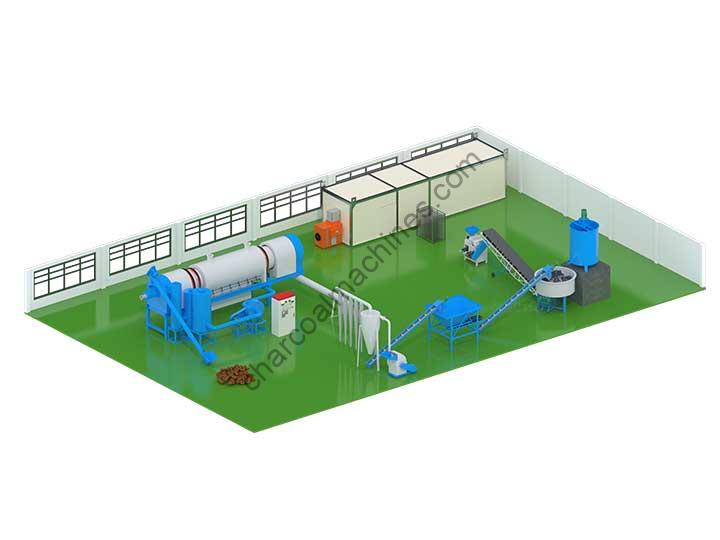
Note: the ball press machine is the key equipment in this production line. Raw materials for this machine can be charcoal powder and coal powder. And its press molds can be changed for making BBQ charcoal with various shapes and sizes. The output of the barbecue charcoal processing line can be customized between 1-20t/h.
BBQ charcoal production line video
Honeycomb coal production line
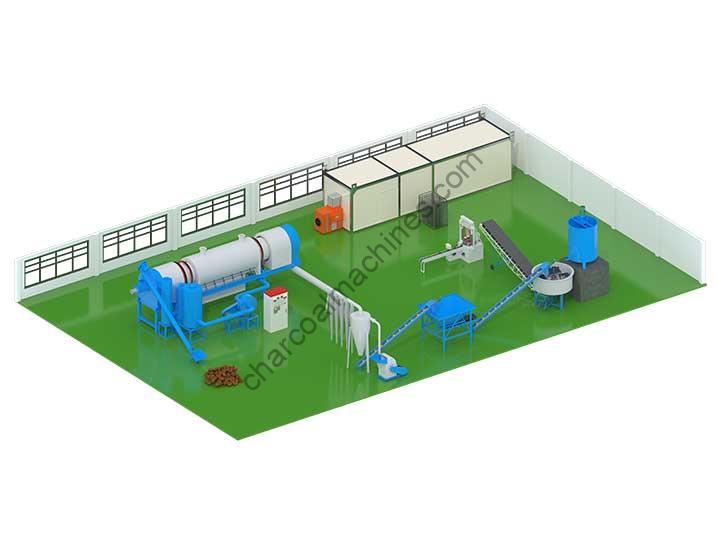
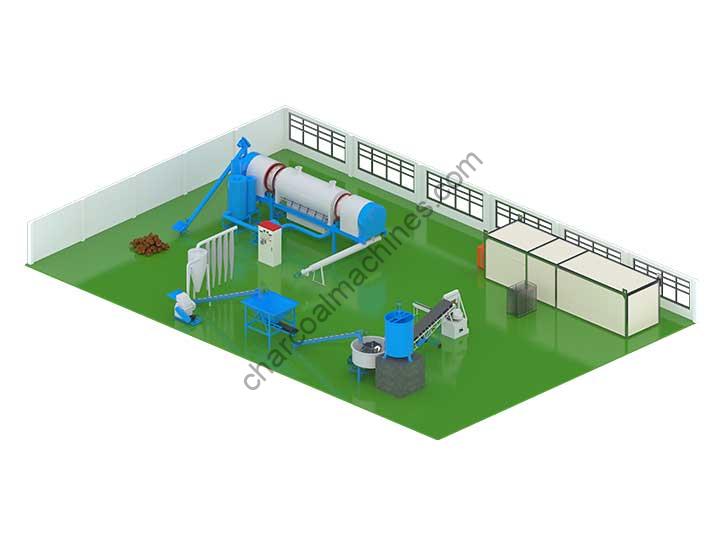
Note: the honeycomb coal forming machine is the main machine in this plant. The raw materials can be charcoal powder, coal powder, rat poison powder, candle fluid, etc. The common shapes of the finished product are mainly honeycomb, square, and hexagon. The honeycomb coal machine is currently very popular in Uganda, Congo, Afghanistan, Vietnam, and other countries.
Honeycomb coal briquettes processing plant video
Main advantages of medium-output charcoal making machines
The medium-output charcoal production line is based on the basic output charcoal production line, the reasonable configuration of some convenient and efficient supporting equipment. Such as a screw feeding machine can achieve the continuous transmission of materials, saving production time.
Replacing the commonly used airflow dryer machine with a large rotary dryer machine can achieve a better drying effect and improve the drying speed of materials. In the process of rod-forming, 5 sawdust briquette machines are used to work at the same time, and the efficiency of the sawdust briquette machine is increased exponentially.
Which can save the time to accumulate finished briquettes, realize continuous carbonization of the carbonizing furnace, improve work efficiency, and greatly increase the output of machine-made charcoal.
Most of the foreign customers who order this medium-output charcoal production line value the potential of the charcoal consumption market in their hometown or even country, followed by the rich raw material market and high rate of return on investment. Most Shuliy customers who purchased the medium-output charcoal production line said: the medium-output charcoal production line has a short payback period, low cost, high production efficiency, and economic benefits.
If you are looking for a more productive charcoal production line…
The output of charcoal making is unable to set the upper limit, no matter how much output of charcoal production line you need, we can give you the best advice! As long as you provide the raw materials and production requirements, Shuliy machinery is fully capable of providing you with a customized version of the charcoal plan according to your investment budget.
Single machine display of medium–output charcoal production line
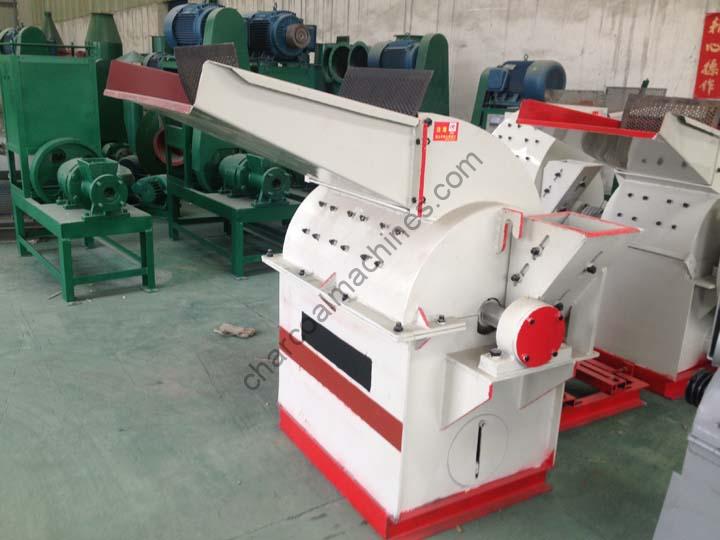
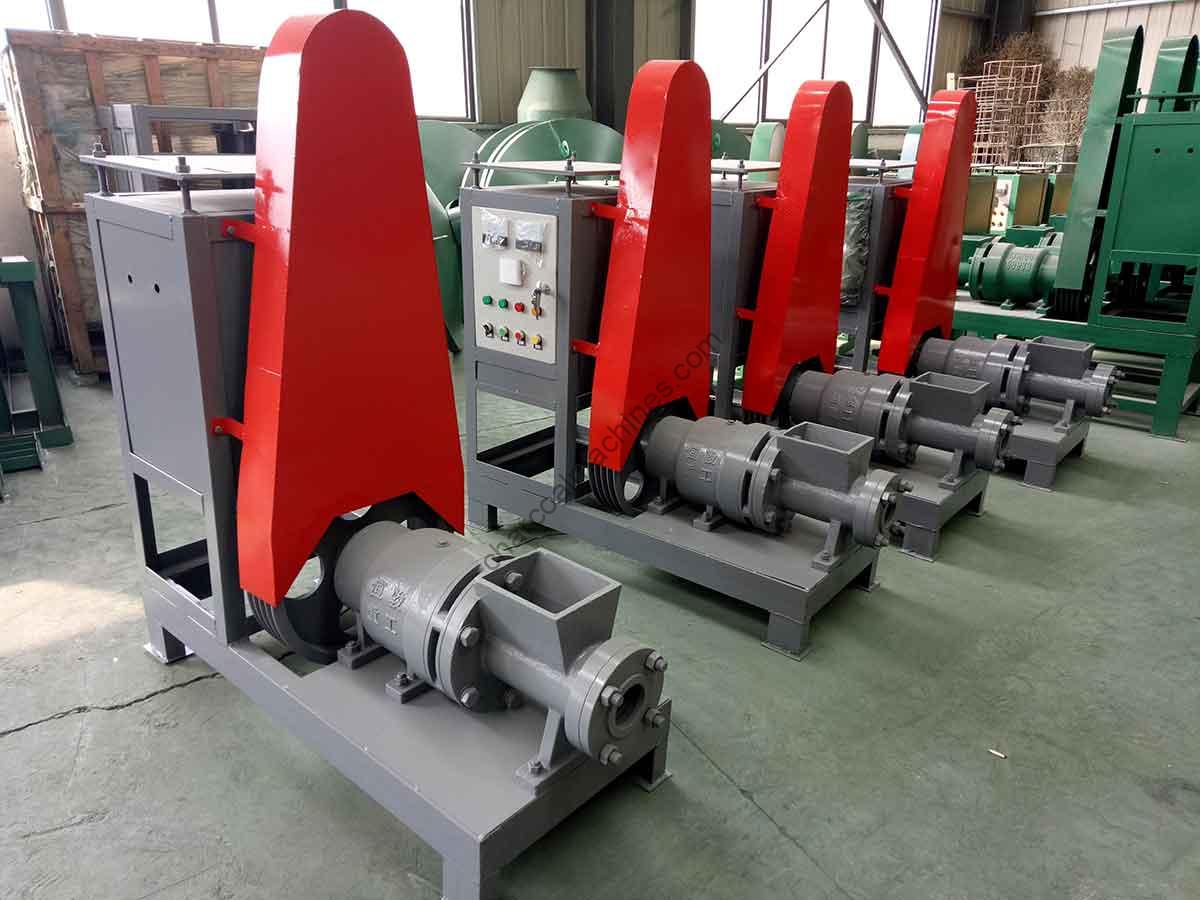
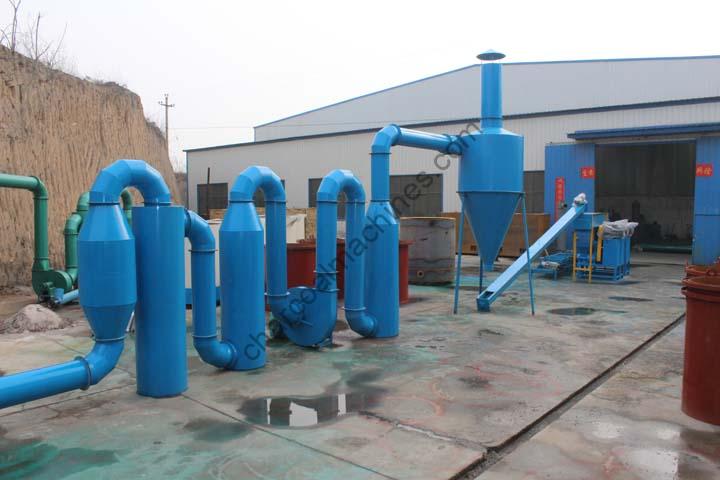
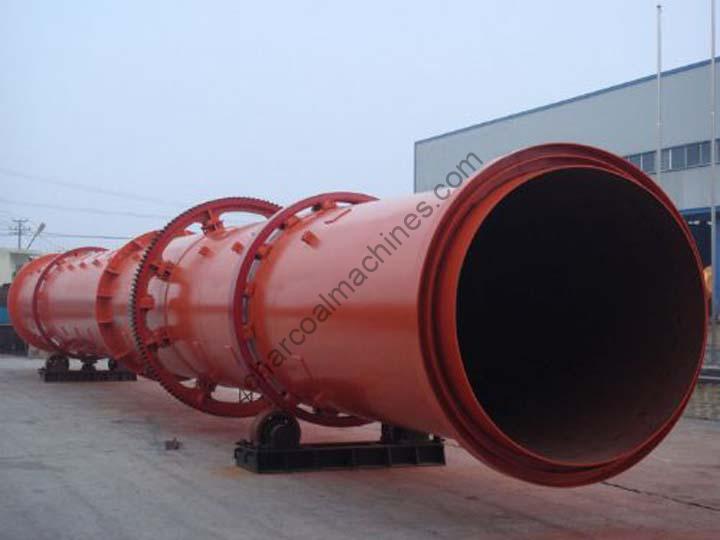
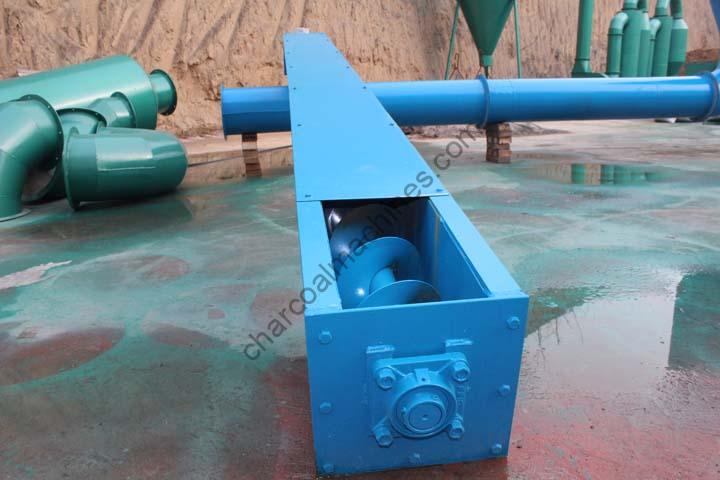
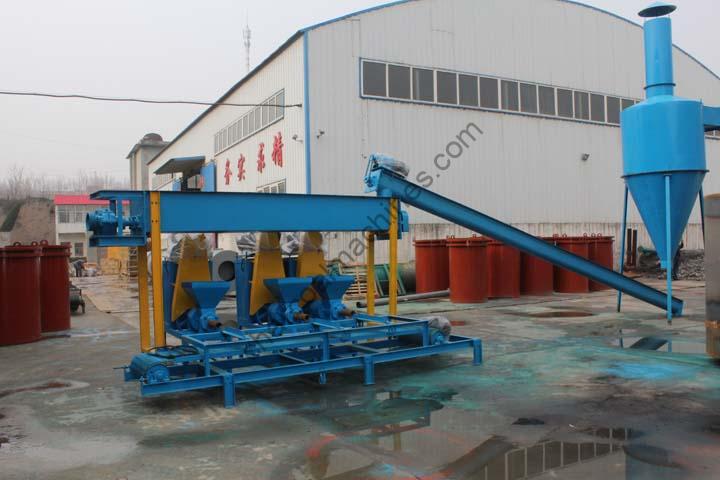
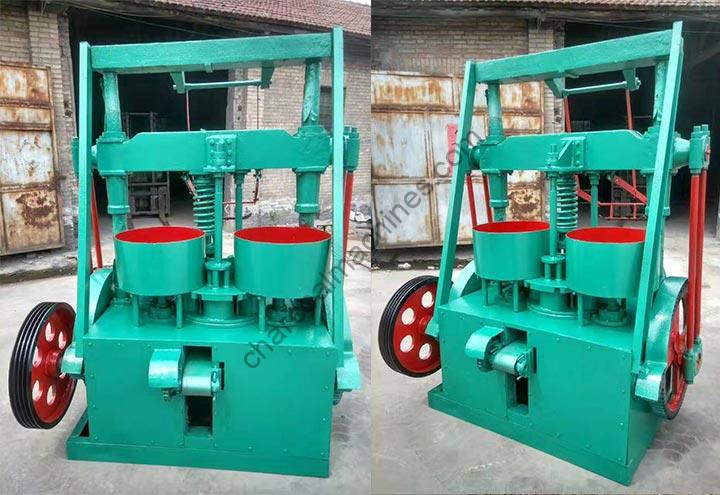
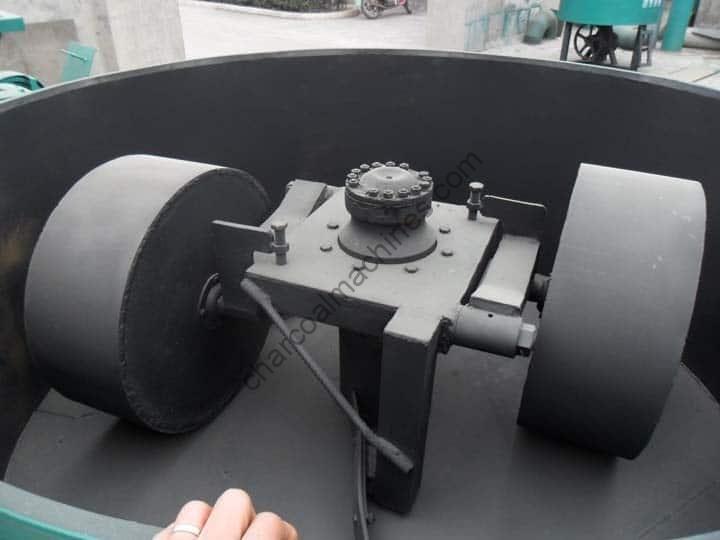
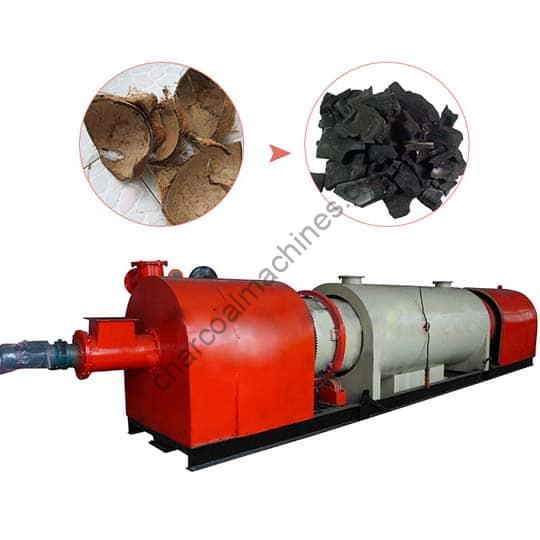
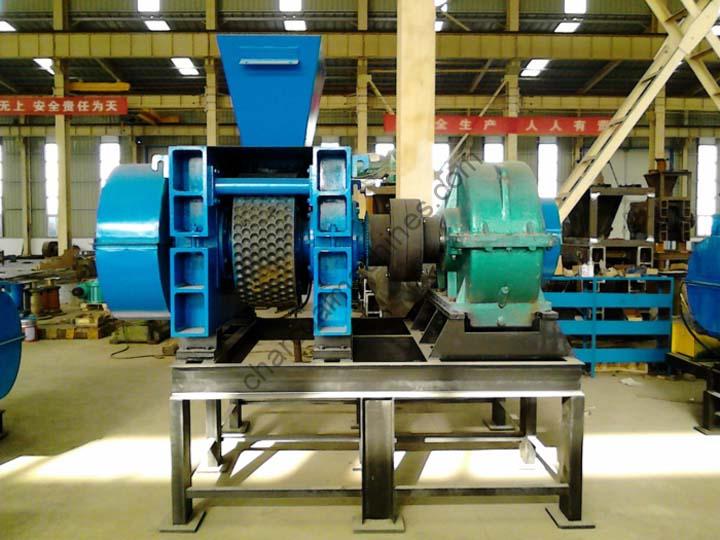
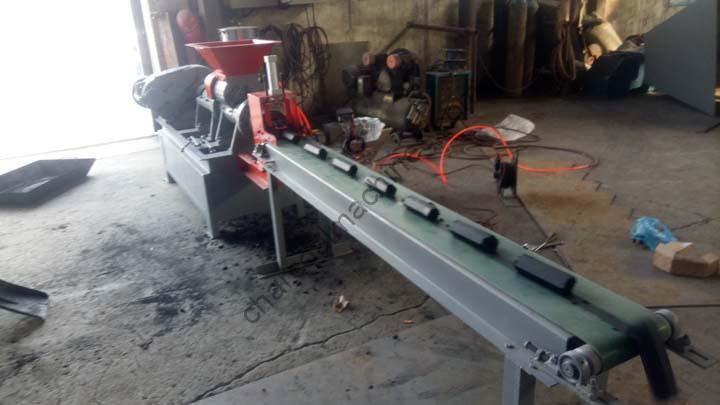
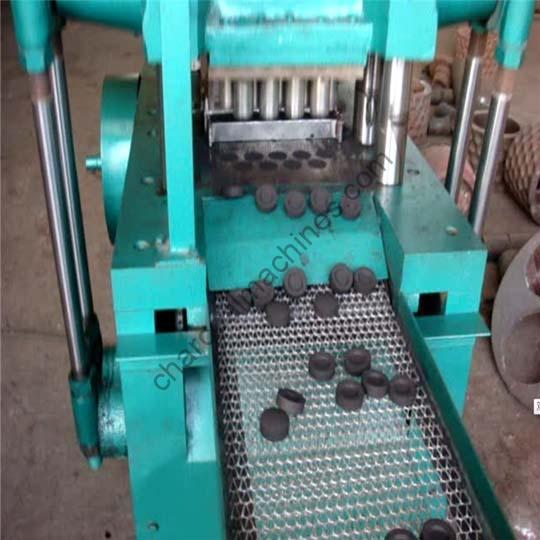
Specific parameters of the complete set of a charcoal production line
NO. | ITEM | SPECIFICATIONS | QTY(SET) |
1 | CRUSHER | SL-1000 Capacity:1-1.5T/H Power:22kw | 1 |
2 | SCREW FEEDING MACHINE | Model: SL-5M Length:5m | 1 |
3 | ROTARY DRYER MACHINE | Model: SL-L1000 Capacity:1.5T/H Size:16000*2600*3800mm | 1 |
4 | SCREW FEEDING MACHINE | Model: SL-5M Length:5m | 1 |
5 | SAWDUST BRIQUETTE MACHINE | Model: SL-500 Power:18.5kw Capacity:300kg/h | 5 |
6 | MESH CONVEYOR | Model: SL-M5 Length:5m | 1 |
7 | CARBONIZATION FURNACE | Model: SLTH-Y Voltage:380v Power:1.5kw Capacity:3T/DAY | 1 |
Why choose Shuliy charcoal machines?
- The reason why the Shuliy charcoal machine has a better experience and longer service life is that our factory adopts more advanced manufacturing technology, which is more accurate in cutting, polishing, and welding steel. In order to ensure product quality, the thickness of the steel we use is 1-2mm thicker than that of the same industry.
- As a professional manufacturer engaged in the manufacture and export of charcoal machines for 10 years, we have processed thousands of orders from domestic and foreign customers. Therefore, we have also accumulated a lot of feedback from customers on their use practices. These valuable experiences are the foundation of our continuous innovation, so our charcoal machine design will be more reasonable, use more convenient, and work efficiency will be higher.
- At present, our factory is no longer limited to providing customers with specific charcoal processing equipment, but to provide a full set of charcoal production programs for different customers. Our team of engineers can carry out plant drawing design, production line matching, profit analysis, etc. based on the customer’s investment budget and production requirements.
- Our sales and after-sales service team are very familiar with the international import and export process, so we will cherish the precious time of our customers and handle their orders properly.
- Due to a certain inventory and strong manufacturing capacity, the lead time of our equipment is relatively short. After delivery, we will deliver shipping information to customers in a timely manner. After the customer receives the goods, we will send a detailed English operation manual and can help the customer to use the equipment correctly through video calls and operation instruction videos.
Charcoal processing line video
Subscribe to our charcoal machine YouTube channel
Charcoal briquettes production line video
Customer visiting of the charcoal business plant
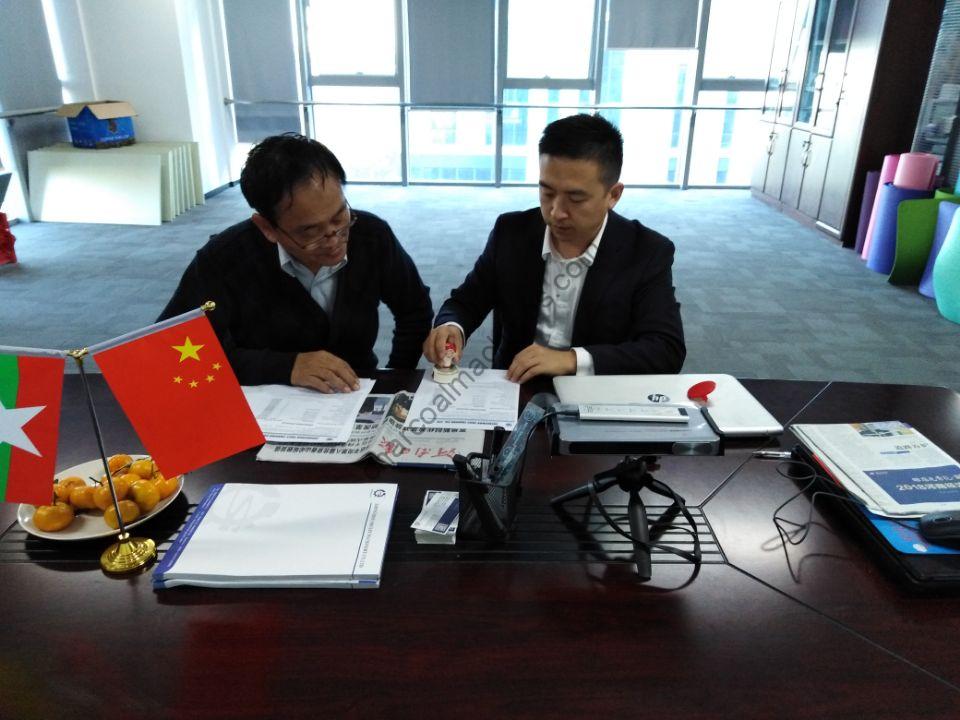
Myanmar customer visiting for the charcoal plant. His factory mainly produces charcoal briquettes from palm kernel shells and branches.
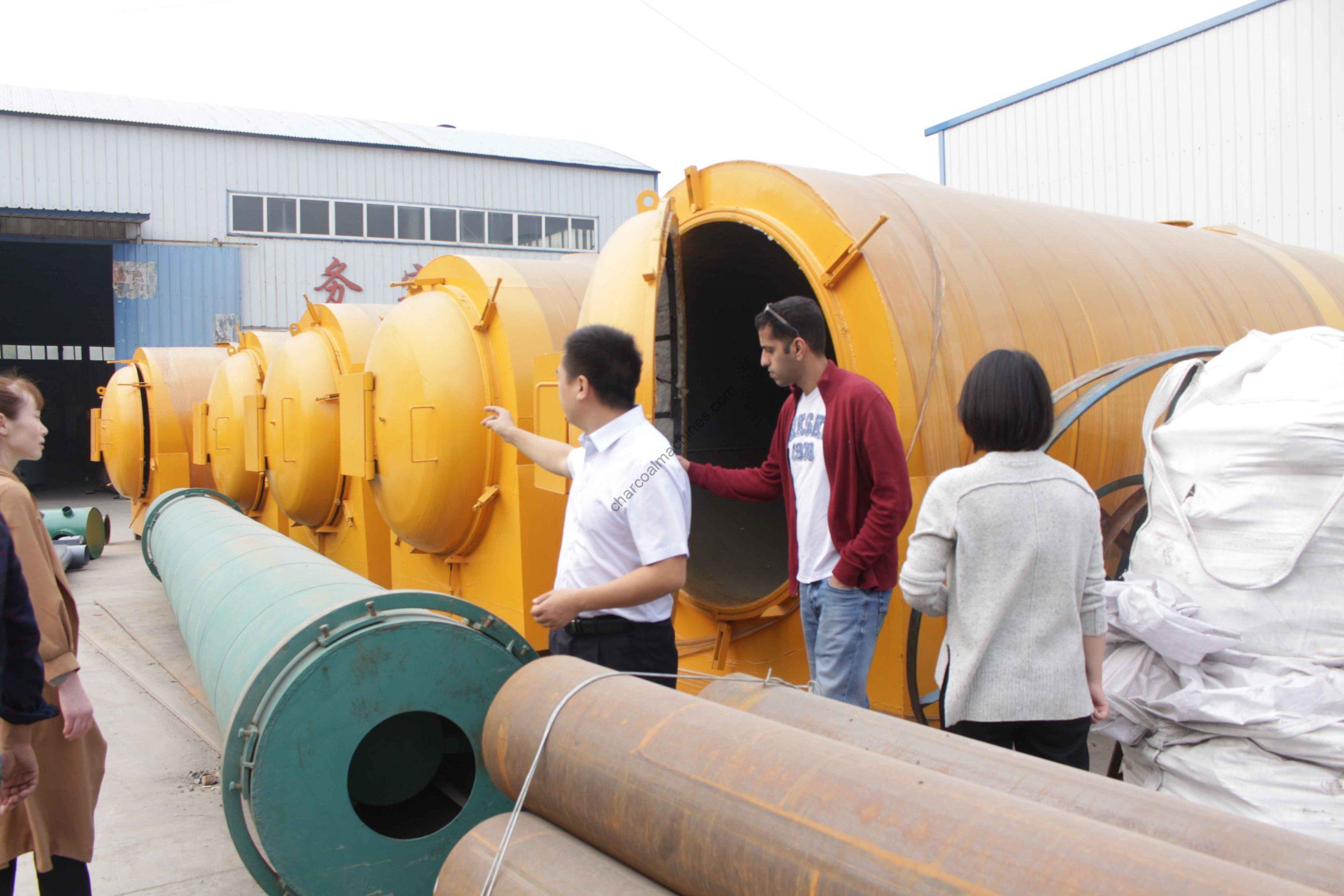
Saudi customers visit the Shuliy factory for shisha charcoal making machines. He and his partner bought the crusher, carbonization furnace, mixer, and shisha charcoal press machine.
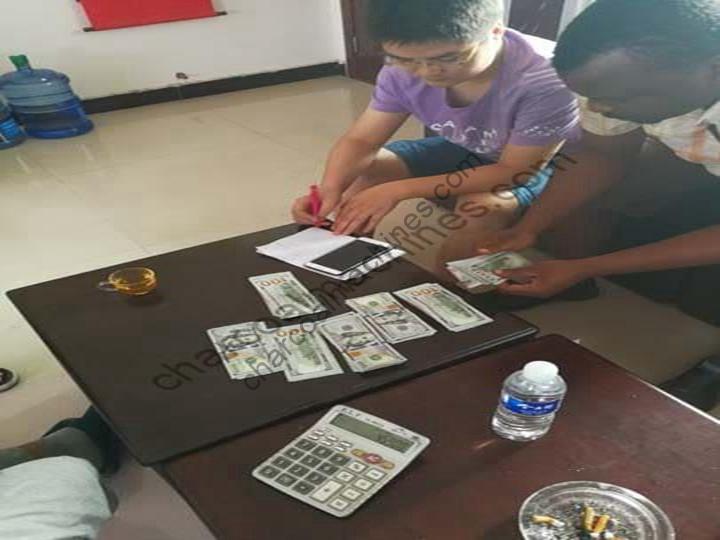
The Nigerian customer came directly to the Shuliy factory with cash to buy the small charcoal line. We provided him with a very cost-effective investment plan.

Vietnamese customers visited the Shuliy factory. They bought a fully automatic charcoal production line with a daily output of 3 tons.
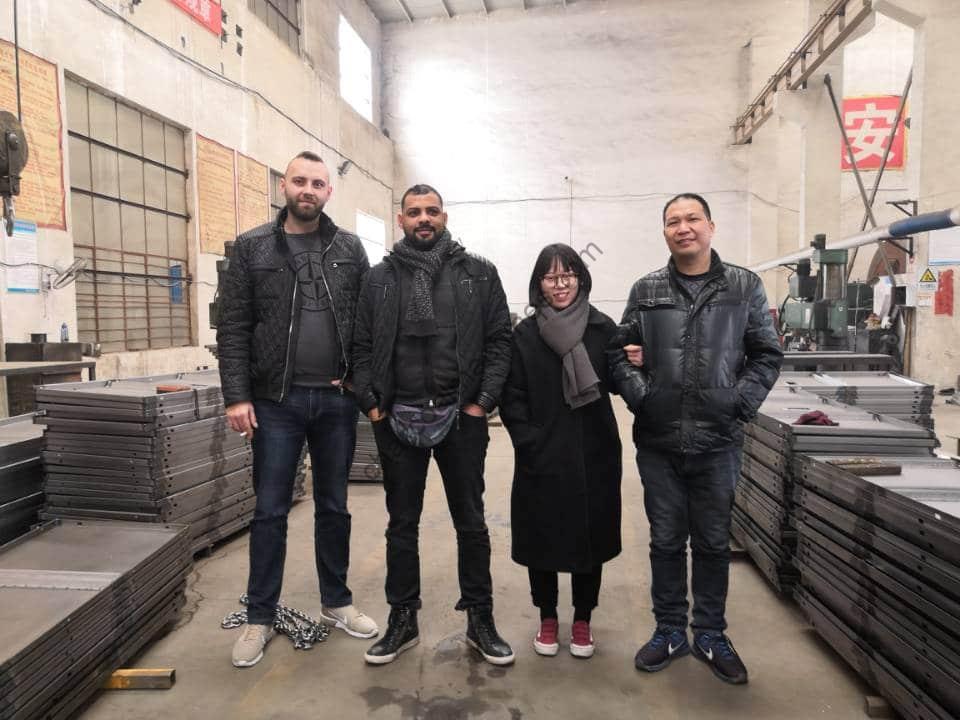
The German customer visited the Shuliy charcoal machine factory. And they finally bought a whole set of shisha charcoal processing plant for making cubic hookah charcoal.
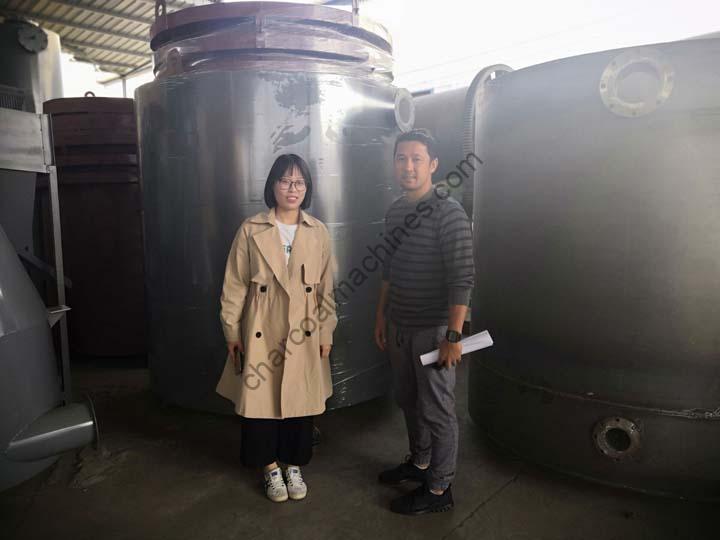
A Filipino customer visited the Shuliy factory. He and his Turkish partner invested in the coconut shell charcoal production business. And they sell the coconut charcoal to Europe.
Contact Shuliy Now!
Thank you for reading this article!
If you have any questions about charcoal making machines and charcoal production solutions, please just call our website customer service phone number (WhatsApp) directly.
And if you find it useful or interesting, please bookmark this article or share it with those in need.
Hot Product
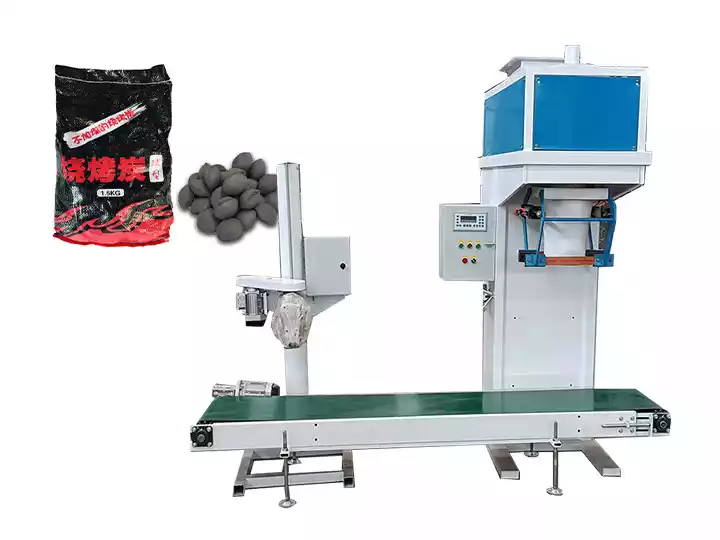
Charcoal Briquettes Packaging Machine for Packing Barbecue Charcoal Quantitatively
This quantitative charcoal briquettes packaging machine can be…
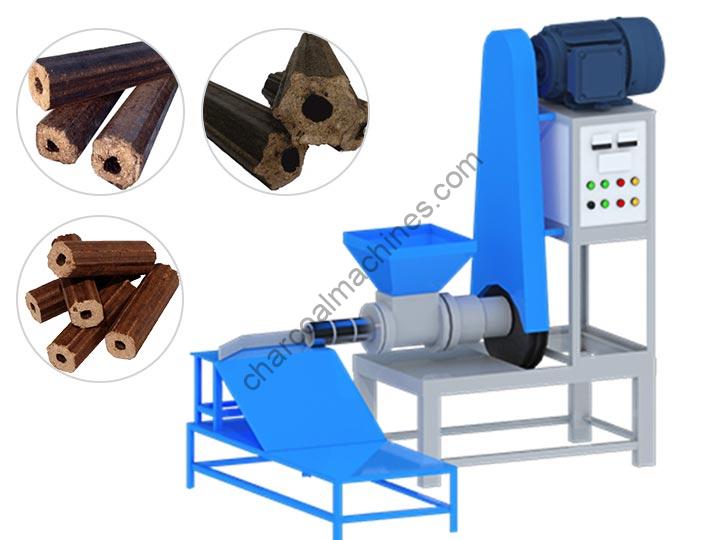
Briquette Press for Making Sawdust Briquettes from Biomass Wastes
The industrial sawdust briquette machine is mainly used to…
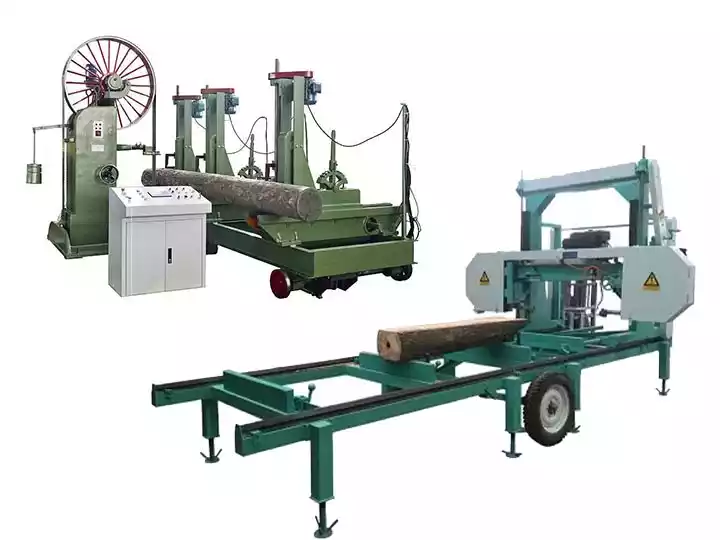
Saw Mill Machine for Processing Lumbers
Industrial wood sawmill machines can saw logs into…
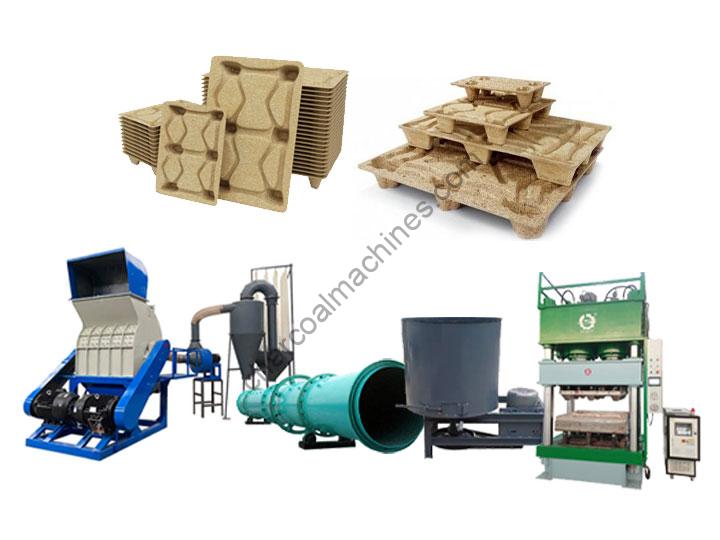
Compressed Wooden Pallet Production Line
The compressed wooden pallet production line is a…
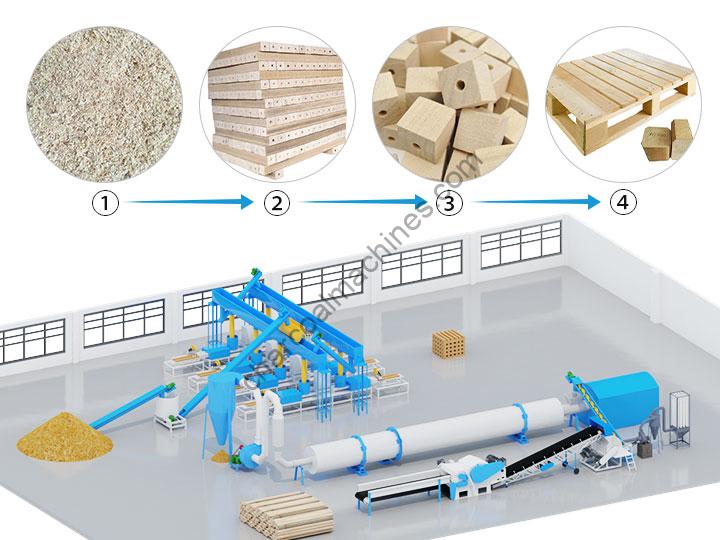
Wood Block Production Line for Making Compressed Wood Pallet blocks
Wood block production line can process high-quality compressed…
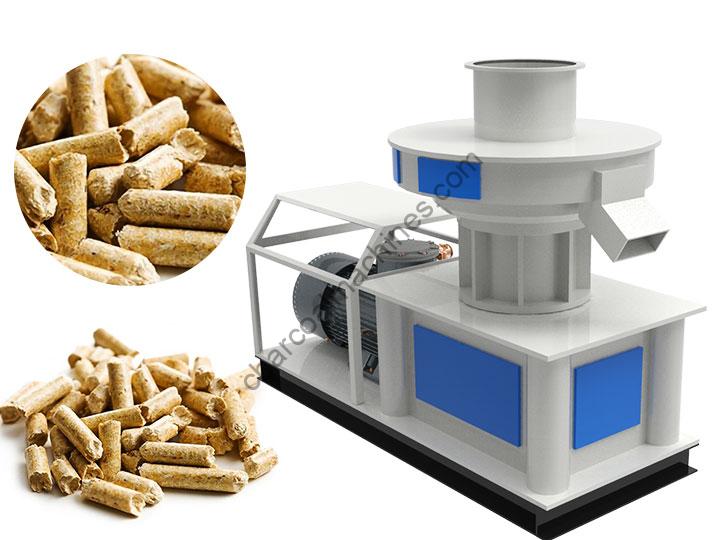
Wood Pellet Machine for Making Biomass Pellet Fuel
Wood pellet machine refers to the compression of…
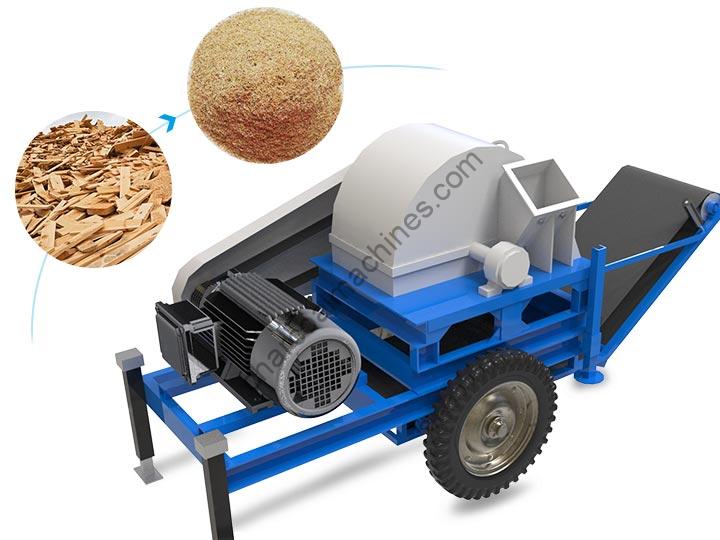
Wood Crusher for Making Sawdust from All Wood Wastes
Wood crushers are commonly used shredding equipment for…
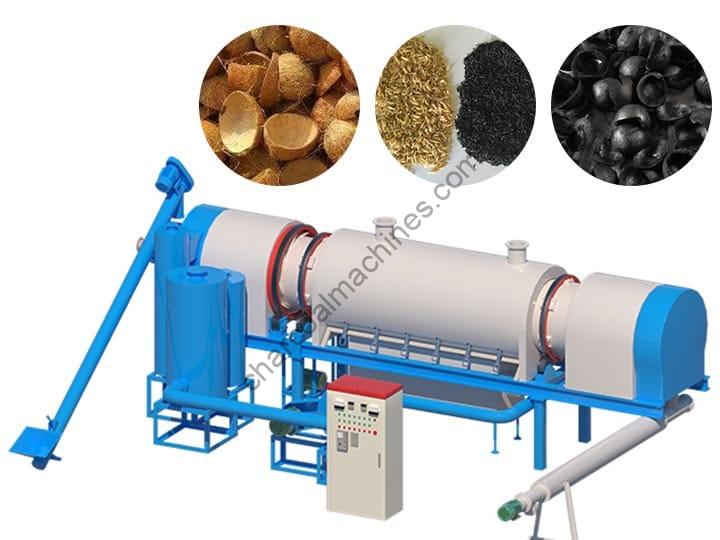
Continuous Charcoal Furnace for Biomass Charcoal Production
Continuous carbonization furnace is a new type of…
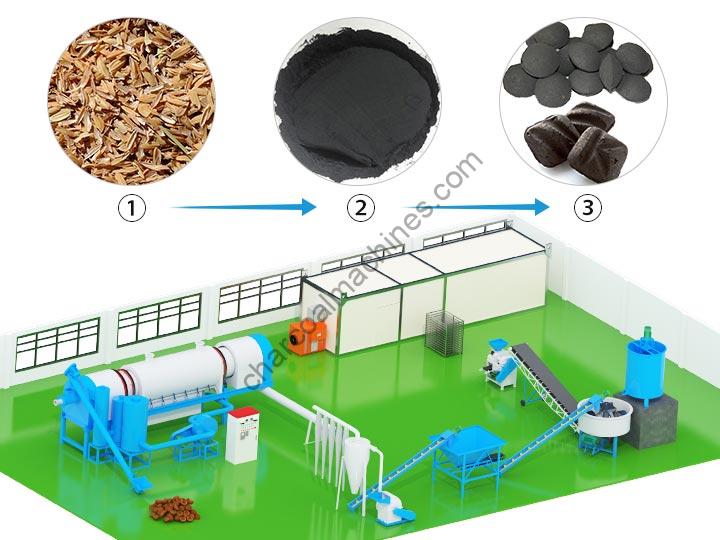
Barbecue Charcoal Production Line | BBQ Briquettes Processing Plant
The barbecue charcoal production line mainly processes various…
26 comments